Zinc CNC Machining
Get instant quotes on custom zinc machined parts with our Online CNC Machining Service. Make quick-turn prototypes and production parts in days with free standard shipping on all US orders. ISO 9001:2015, ISO 13485 and AS9100D certified. ITAR registered.
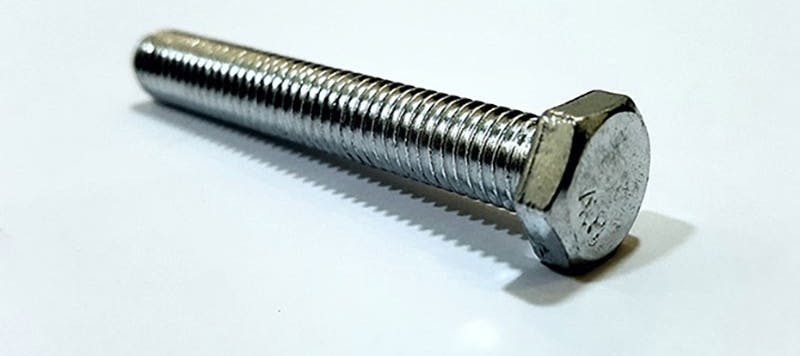
Zinc CNC Machining
Zinc (denoted as Zn on the periodic table) is a relatively common non-magnetic metal. It is typically alloyed with aluminum, magnesium, and copper. This class of zinc alloy is referred to by the name Zamak (the term originated as an acronym for the element names in German: “Zink, Aluminium, Magnesium, and Kupfer”). These alloys are usually supplied in the form of ingots due to their extensive use in die-casting applications. Zinc has excellent damping capacity; it is highly ductile and exhibits long-term dimensional stability. Die-cast Zamak alloys maintain high levels of precision and therefore require less machining to bring the part into the required tolerances.
Zinc alloy metal is some of the cheapest materials available. Despite a low price point, they have good mechanical strength, are easily machined, and resist mechanical shocks well. Complex components are often initially die-cast and then have critical features machined into them, reducing overall CNC machining time and cost. The automotive industry makes extensive use of CNC machined zinc alloys.
Zamak 3 (Zinc alloy 3)
The Zamak 3 alloy contains 4% aluminum while less than 1% is composed of copper and magnesium. Zamak Zinc alloys exhibit similar machinability to copper but are less abrasive to tooling. Automotive part shells and small electric motor casings are typical applications for this type of zinc.
Tensile Strength, Yield (MPa) | Fatigue Strength (MPa) | Elongation at Break (%) | Hardness (Brinell) | Density (g/cm^3) |
---|---|---|---|---|
Tensile Strength, Yield (MPa) 208 | Fatigue Strength (MPa) 48 | Elongation at Break (%) 10 | Hardness (Brinell) 82 | Density (g/cm^3) 6.6 |
Finshes and Post-Processing Options
Zinc alloys respond well to a wide range of surface finishes. Some of the more common finishes for CNC machined zinc are listed below:
Chrome Plating: Zinc alloys are ideal materials for cosmetic applications due to their low price points. They are easy to chrome-plate in order to create parts with the feel and look of polished stainless steel at a fraction of the cost.
Chromate conversion coating: Not to be confused with chrome plating, this process involves placing the zinc part in a chemical bath that will react with its surface. This reaction results in a part that is resistant to light chemical attacks. Different chromate compounds offer differing levels of corrosion protection and result in different colors.
Painting: Zinc is readily painted as long as it first receives the right pretreatment. There are various ways to make paint adhere better to the zinc’s surface. These include phosphate conversion coatings or zinc chromate-vinyl butyral primers. Once the surface is prepared, painting is simple.

Cost-saving Design Tips
Zinc is a cheap material, so at least some cost savings are built-in. However, to further leverage these savings, refer to the tips below.
Casting: Depending on the volume of components required, expenses may be reduced by casting the part and then only machining critical dimensions and features into it.
Non-critical parts: Zinc is ideal in applications where plastics won’t suffice but cost still needs to be kept to a minimum. Zinc alloys eliminate the need for advanced plastics and offer better long-term dimensional stability.
