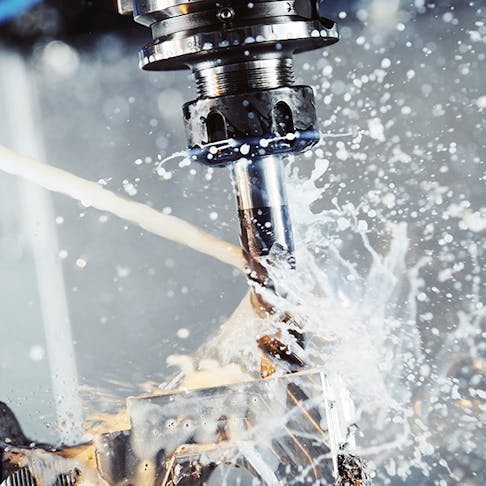
Tackling Drill Bits Part 01: Drill Bit Breakage and Tool Life
Have you or your loved ones been personally victimized by broken drill bits, bad tolerances or terrible finishes? We’ve put together a list of common drilling issues machinists might run into, as well as some of the causes and fixes that might help you get up and running again.

Have you or your loved ones been personally victimized by broken drill bits, bad tolerances or terrible finishes?
We’ve put together a list of common drilling issues machinists might run into, as well as some of the causes and fixes that might help you get up and running again.
Naturally, you should first make sure you’ve purchased a quality drill bit. Quality work never happened with cheap tools. Another good rule of thumb in drilling is to start cautiously with a moderate speed and feed, taking careful note of your drill’s action and condition before increasing either with confidence. (Arguably, this applies all situations in life, but that’s another conversation). Starting out carefully can help you identify and fix issues before they cause mistakes in your work.
First Issue: Broken Drill Bits
A broken drill bit is a very common problem, and it’s an issue that has many possible underlying causes and symptoms. Again, the first thing you need to make sure of is that you’re using the right drill and point in the first place. Double-check your lip clearance angle as well. This may seem obvious, but hey, acting like a dunce doesn’t mean you’re not smart as heck (or at least, that’s what I tell myself). If you’ve got those things squared away for sure, then the fix might be less obvious.
If your drill bit is binding in the hole, make sure to check that your drill bit is sharp. If either the point or outer corners are dull, then you’ll need to do some maintenance. This might mean re-pointing or replacing the drill bit, and checking your coolant type and amount. That being said, if you sharpen your drill bit you do risk taking the coating off. Depending on what job you’re doing, you might be better off ordering a replacement.
If your drill bit is binding and the flute is clogged up with chips, consider a drill with more generous flutes, a faster helix angle, or possibly polished flutes (to reduce friction). You may also need to start withdrawing the drill at intervals to clear the chips away. Also consider heavier feeds or switching to a chip breaker drill design.
Your drill bit also may break if your work is insecurely held. Embrace those drill bits with better clamping and holding in order to prevent broken drills as well as irregular holes. Excessive feed pressure is another reason why your drill bit might be chipping and breaking. As you can imagine, reducing your feed is a good fix to that (I’ve also heard deep breathing helps).
Second Issue: Chips Not Breaking
If you’ve got a build-up of chips clogging your workpiece or strangling your drill bit shank, you know you’ve got to make a change, or risk drill bit breakage. Depending, this can also become a workplace safety issue. By keeping an eye on the way your chips are forming and/or obstructing your work, you can usually make a faster diagnosis. Chips shaped like Cs and 9s are ideal, or longer conical spirals. If you’ve got fan shapes, needle shapes, zigzag shapes, or irregular segments, you need to do some detective work. Actively listening to your drill is another way to catch issues before your workpiece, your drill bit, or even your drill are damaged. Usually, chip issues require adjustments to speed and feed, though you should also be sure you’ve applied sufficient coolant, cutting fluid, and/or lubrication.
You may need to experiment a little with higher and lower feeds. Though you should always work within the parameters your tooling provider suggests, making adjustments and taking notes will help you find and remember the best ratio of speed and feed.
Your tool geometry is also a factor. A chip-breaker design drill and/or chip-breaker point grind can be valid options if you find you need something a little more specialized.
Third Issue: Poor Tool Life
Your drill bits are always going to experience wear and tear, but your setup and the way you treat your tools can have a definite effect on their longevity. If your drill bits have more craters than the moon, your surface finish is shot, or you’re experiencing unjustified flank or edge wear, you might need to make some changes to increase the life of your tools.
Cranking your speed and/or lowering your feed too much are great options if ruining drill bits is your goal. Calculating your speed and feed does require a bit of math, some note-taking, and a bit of astute observation, but taking that time will produce positive results.
That being said, you may also need to double-check that you’re using the right tools for the job at hand. The wrong point type, or even just the wrong drill bit for the application, can cause some serious screwups (or twistups?! Eh??). Review the conditions you’re working under and compare them to the point type and drill bit you’re using. Simple as that, but jeezle pete can you save yourself some forehead smacking and foot-stomping.
Fourth Issue: Oversize Hole
If your tolerances are being shot by oversized holes, there are a few possible causes you might check on. First, make sure your workpiece is securely held and tightened to rule out any vibration or other movement on that end. Next, make sure that your drill point is true to center. If it’s off, you may need to re-point it with an eagle eye to accuracy, or perhaps you need to just replace the drill bit entirely. Additionally, make sure that after you drill a hole to your specifications, you immediately back the drill out and shut the machine off. Running a drill in the hole after its cut will result in an oversized hole.
If none of those problems seem to be the issue, your machine spindle might be the culprit. Test to see if it's rigid enough and running true. Fixing this might mean simply implementing a better cleaning and brushing routine before machining, or possibly following through on some machine maintenance.
Join us in Part 02 for a look at tackling more drill bit problems such as chipped lips, damaged points, and more.
