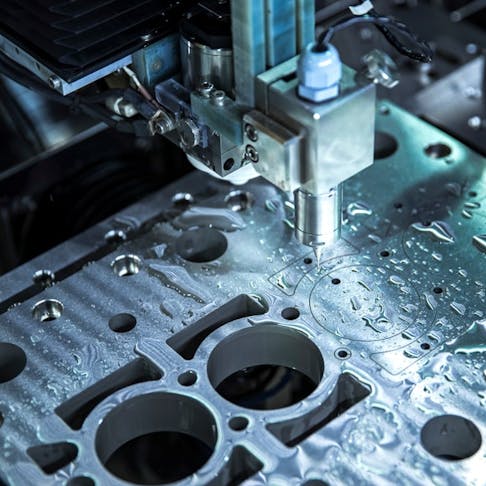
How to Limit the Effects of Temperature on CNC Performance
Temperature, especially during the hotter summer months, can have a profound impact on a CNC machine’s performance. This article will review 2 factors that affect CNC temperature and offer 4 tips to keep your CNC machine cool.
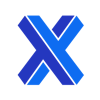
Temperature, especially during the hotter summer months, can have a profound impact on a CNC machine’s performance. CNC machines can run for hours with no stoppage to complete one part. This enables an excessive amount of heat to develop in the workpiece, tool, and machine itself. While increased temperatures in the CNC machine have the potential to cause damage to CNC machine components and computers, increased temperatures in machine tools can lead to thermal deformation - causing diminished form and machining accuracy. This can potentially lead to dimensionally defective parts, excessive downtime, and consequently, reduced profits. There are many factors to consider when determining how best to limit the effects of excessively high temperature on CNC-machined parts: from the CNC machine itself to the frictional forces generated at the tool/work interface. This article will review 2 factors that affect CNC temperature and offer 4 tips to keep your CNC machine cool.
Two Factors that Affect CNC Temperature
To better understand how you can limit the impact of high temperatures on CNC components and machine tools, it is important to identify the factors that affect it. Below are the main factors that affect both the CNC machine’s temperature and the temperatures at the tool/ work interface:
1. Climate and Machine-generated Heat
Typical machine shops are a beehive of activity, with multiple CNC machines, computers, forklifts, heat-treating ovens, and other equipment all running simultaneously. Each one of these generates heat that the facility's air handling system must remove. Whether you’re running a shop in an arid desert or in a very humid region, it’s important to maintain a comfortable ambient temperature within the facility. Sustaining this comfortable temperature, however, is more easily said than done when several machines are running simultaneously.
If the ambient temperature becomes too hot, it not only affects the health and safety of your workforce but can also impair the productivity of your CNC machines. From excessive tool wear to damaged computer systems, the effects of excessive heat and humidity can be devastating. Thankfully, temperatures can be regulated within manufacturing facilities by a variety of methods - from ventilation to evaporative cooling to central air conditioning.
2. Material Properties
The material properties of the tool and the work have a major impact on localized heat generation. Ultimately, the goal is to control the temperature of the tool and workpiece to maintain dimensional stability of the final product and prolong tool life. Running a CNC operation for hours on end generates an intense amount of heat in both parts. Heat-related physical properties such as the coefficient of thermal expansion, thermal conductivity, and specific heat, will dictate how fast a particular material will increase or decrease in temperature.
For example, cemented carbide tools generally perform better than high-speed steel tools over long machine runs. This is due to their ability to retain high hardness and strength even when exposed to high temperatures. Conversely, workpiece materials commonly used in machining such as aluminum are more sensitive to heat and can change temperatures drastically. This leads to more quality issues as temperatures increase due to inadequate chip removal and dulling of tools, among other things. When it comes to CNC temperature, it’s important to consider the material properties of both the tool and workpiece to balance both efficiency and quality.
Four Tips to Keep Your CNC Machine and Tools Cool
The following tips can help you regulate both the CNC machine and tool’s temperature based on manufacturer recommendations:
1. Facility Cooling
Maintaining a cool temperature can help tremendously in keeping CNC temperatures down. Centralized HVAC systems, though they can be expensive, are effective at reducing humidity and removing warm air from a facility. Depending on the climate at your factory's location, you might decide on an evaporative cooler, one powerful centralized AC unit, or a distributed AC system consisting of a series of smaller units to cool different zones in the facility to different levels.
If centralized HVAC or evaporative cooling systems are too costly, consider using a series of industrial fans fixed to the ceiling and other high points like columns or banisters throughout the facility. Then, couple these systems with blowers that force air outside of the facility. The fans at the high points of the building will produce air movement that prevents pockets of hot air from developing while the blowers completely remove the hot air from the building.
2. Conduct Maintenance Regularly
Following a methodical, routine maintenance schedule for your CNC machines can help prevent temperature excursions from becoming an issue. Checking for leaks in air and oil lines, verifying spindle alignment, and refilling oil and coolant levels, for example, are some of the ways you can care for your machines and prevent them from overheating. Especially during the hotter months, check, clean, and/or replace the fans and air filters on computers and machines throughout the facility. Airflow is essential to cool computer systems and equipment. Keeping fans on your machines and equipment cleaned and maintained also helps tremendously in limiting the effects of high CNC temperatures.
3. Use a Cooling Medium During Machining
Coolant use plays an important part in both chip evacuation and cooling. There are 4 main types of mediums that can be used during machining to cool both the tool and the workpiece:
- Air (via jet or stream)
- Misting
- Flooding
- High-pressure spray
Each of these cooling methods has its own advantages. Air effectively cools and removes chips, but is not as good at providing lubrication. This type of cooling is most suitable for parts that are sensitive to direct cooling - particularly plastic parts. Mist and flood cooling are both low-pressure forms of cooling. Mist is a great option when chip evacuation and heat are not big concerns - as in, the heat generated in the tool and workpiece are not detrimental to the final product but you would still like to provide cooling to prolong tool life. Flood cooling, on the other hand, is a low-pressure cooling form to use when chip evacuation and heat are a concern.
High-pressure air or liquid is perhaps the most common method for cooling CNC machines. It is extremely effective at both removing chips and cooling the tool and workpiece but has the potential to break small-diameter tools if it comes in direct contact. High-pressure spray cooling is often used in deep-drilling or long-running cutting processes. It’s important to pick the type of cooling that is best for your operation.
4. Clear Chips From the Machine
Metal chips removed from a workpiece can be exceptionally hot due to the forces experienced during machining. If enough of these chips accumulate in one place, it can become a thermal reservoir that can transfer heat into the rest of the machine and tooling. Additionally, an abundance of chips can stick to cutters and workpieces, causing quality issues and lost production time to clear chips and or jammed tooling. Therefore, it is important to ensure effective chip removal methods are in place. Using a form of air or liquid high-pressure cooling, coupled with a conveyor that automatically removes chips, is a great way to maintain control of temperatures in CNC machines.
Keeping CNC Machining Cool
People can cool themselves off with a glass of ice water or by taking refuge in the shade. Just as people take care of themselves in the heat, it’s important to also take care of CNC machines in the heat. Keep your CNC machines cool with the tips presented in this article. Contact a Xometry representative today to discuss how we can assist in ensuring that your CNC machines stay within their optimal temperature range for efficient operation.
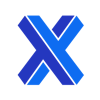