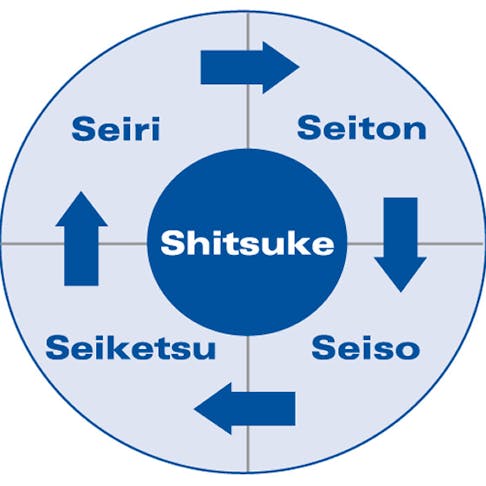
5S Principles in Lean Manufacturing
5S is a five-level routine designed to create a more productive and orderly work environment.
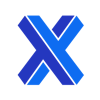
5S in lean manufacturing is an operational tool that developed in the Japanese automotive sector, promoting and operationalizing “best practices” in a factory. It has broadened into a set of principles for all areas of business, but with mixed outcomes. Nobody thinks “best practice” is a bad idea, but how to achieve it and keep achieving it is a challenge.
5S and all the systematic quality/efficiency systems that preceded and are following it (for example, the Toyota Production System and Total Quality Management) have one purpose—to reduce wasted effort now and in the future. In short, to make efficient companies that thrive. The word “lean” summarizes the core ideas that are at the heart of successful companies' approaches. Easily summarized as, “do only that which is productive”:
- Design out overburden, deadweight, and effort that doesn’t contribute to productivity.
- Design out the inconsistency, the potential for variance/error, and the risk of random or out-of-specification moments.
- Eliminate waste, breakage, and variances.
5S History and Definition
The 5S in lean manufacturing originated as 4S in the 1980s, from TPS (Toyota Production System), which became 4S, with 4 of the 5 same S’s and had the (English) acronym R.I C.K in some areas: Remove, Identify, Clean, and Keep clean. It didn’t take very well and quickly got the 5th S (Seiketsu (清潔)), an updated translation, and rolled out widely.
5S is a five-level routine that creates a more productive and orderly work environment. In broader interpretations, 5S principles have become foundational for implementing lean production tools and processes in almost any activity. 5S originated as a codification of order, a place for everything, and everything in its place. Now things and places can be virtual and can be processes and systems that are distant from a factory. The meaning of each S is:
- Seiri (整理)/Sort: Eliminate that which is not needed. Remove from the workspace and put into storage the things that are not in use.
- Seiton (整頓)/Straighten: Organize what remains after sorting. This describes assigned locations and labels for everything in the workspace (and virtual spaces).
- Seiso (清掃)/Shine: Clean and inspect the work area. This principle requires staff to tidy and evaluate their workspace for issues to be addressed—stock required, broken or missing requisites, and opportunities for improvement.
- Seiketsu (清潔)/Standardize: Write and follow standards for 5S. It is agreed upon as the reinforcement and allocation of responsibility for housekeeping activities and regular reviews/audits.
- Shitsuke (躾)/Sustain: Consistently apply the 5S standards.
Why Do Some 5S Implementations Fail?
Put simply, 5S in lean manufacturing is simple to understand and hard to execute. The top-three reasons 5S implementations succeed are:
1. Getting Buy-in at All Levels
In companies and teams in which there is full buy-in and enthusiasm, implementations generally create benefits. The majority must want it to succeed and know why. Real commitment is the first hurdle.
2. Great and Visible Tracking/Discussion of the Benefits
Well-operated rollouts gather momentum if the positive outcomes are shared and celebrated. 5S is not decorative, it is a functional and integrated effort to cut costs and improve service/outcomes. Tracking all benefits from 5S will help to maximize the chances of its success.
3. Good Leadership
5S implementations need consistent steering. In the early stages, team members will find low-hanging fruit to improve quality/productivity. And this needs a great core team steering changes methodically, strategically, and in a systematic way that minimizes disruption and maximizes team understanding of the process and the outcomes.
Why Is 5S So Important in Manufacturing?
While the systems that spawned 5S were first developed in the auto industry, it is now viewed as an essential element of lean manufacturing, regardless of industry. Operationalizing 5S as a pillar within a company or team does not only mean improved cleanup habits and smoother process flows. The methodology encourages wide-ranging improvement in the overall work environment and reduces wastage (muda). When done right, 5S is a low-cost, low-friction, high-impact mindset in manufacturing that empowers the people who do the work to figure out how to do it better. It teaches (trains) team members that they own their workspace and outcomes. When done well, 5S influences outcomes in profound ways.
Specific Benefits of a 5S Program and How To Implement It
A simple review of working-environment benefits and the flow from the improvements result in some easily understood wins that everyone can benefit from, including:
- Freeing space by improving storage habits.
- Saving wasted time by organizing/optimizing workspaces.
- Improving productivity and quality by pre-maintenance of equipment.
- Increasing team engagement by making everyone responsible for their space and process.
- Reducing accidents and staff health risks by addressing issues before the crisis.
Step 1. Seiri (整理)/Sort
The sort stage differentiates needed tools and materials in the work environment from those that are not, or may not soon be, needed. Idle items are marked (“red tagged”) and moved to a holding zone. Listed below are four categories in the sorting of items in materials:
- Items required for current work to proceed.
- Items required in another work area or from a central reserve or on-hand store, and also misplaced items.
- Items that may be needed.
- Items that are not required.
There are various approaches to the red-tagging of documents, data, comms history, and software. Companies needing to implement this aspect of a 5S system must tread carefully. Imposing order can have unintended consequences and should be approached in a careful and reversible way. Some clear examples of sort actions are:
- Remove waste materials and discard them.
- Dispose of broken, worn, or otherwise obsolete parts—using red tags, if other staff may need to review.
- Recycle materials and paper, accounting for proprietary information in the disposal of documents.
- Handle storage of everyday tools and materials appropriately; ditto for special and irregularly used tools.
- Avoid storing excess materials; return to stores (if allowed) or use a red tag.
Step 2. Seiton (整頓)/Straighten
The straighten step imposes a planned orderliness to that which remains after the sort. Such items should have a well-understood “rest” position to which they can be returned after use or at the day's end sort. This doesn’t generally require the famous tape outline for a stapler on the team members' desks! Though shadow boards for tools are almost universally appreciated. Allowing individuals authority over their space is key to making 5S function. Each “owner” of an area must be empowered to do what they see as representing the most value to them first and then to the team. Mentors and auditors can advise as to best practices, but the owner of the area must actively support any changes. Enforced order will not be natural, and represents one of the “trigger” points for resistance.
The straighten has a simple purpose: needed things returned to a rest position can be found when needed again. This reduces time spent hunting in the clutter, especially when items are placed in operation-friendly and ergonomic rest places. Implementation of the straighten generally needs a version of this methodology:
- Place the most-used tools and materials (real or virtual) within the easiest reach.
- Group tools and materials into logical categories.
- Visualization of rest places can be useful, if not over-specified.
- Use containers such as kanban bins.
- Use labels if there might be doubt.
- The initial straighten will not be the last. Be flexible in revisiting the straighten.
Some clear examples of straighten actions are:
- Give everyday things a defined rest place.
- Color code to give a glance clue.
- Place everyday things at the easiest and most task-appropriate places; less regularly used things can be placed less conveniently.
- Try to assign one area entirely to straightened storage, unless task areas with specialist inventory are not all in one place.
- Clear the “work” area of every distraction, and store nothing there except immediate-use things.
Step 3. Seiso (清掃)/Shine
The shine is sometimes referred to as elevating the work area by thorough cleaning and inspection. The “elevation” is an arguable concept that sometimes gets wrongly thought of as beautification. This stage includes performing routine maintenance on equipment and the workspace infrastructure.
The implementation of shine creates a clean and work-ready environment that most people will enjoy. Perhaps, most importantly, it allows the owner to rapidly identify maintenance issues before they affect productivity. Implementing shine simply requires end-of-day or end-of-work-block cleaning, inspection, and routine maintenance:
- Take cleaning seriously. It encourages a close evaluation of every item you touch/clean, and you can use the opportunity to be ready for the following day or work block.
- When you find trace evidence, find the source. Trace materials can indicate a problem that can be solved early.
- Look closer, while cleaning everything. Review it and examine its condition. It might require an update or maintenance.
The real benefit of the shining stage is to gain information about problems early. But looks should not be a substitute for function. Beauty rarely equates to efficiency. Some good examples of shine actions are:
- Sweep and/or wipe down tools, equipment, and work surfaces.
- Examine everything for wear, faults, and functional issues.
- Regularly inspect larger machines, removing covers if required, to confirm the state of their parts.
- Investigate causes of recurring contamination.
- Follow procedures and use appropriate agents to prevent damage.
Step 4. Seiketsu (清潔)/Standardize
The standardize stage is in many ways the hardest. It is the glue that holds 5S together, long-term. It is the link between sort, straighten, and shine and the final and most important step, sustain. The purpose of the standardize step is to capture and codify the practices developed in a rollout of 5S as standard operating procedures (SOPs). Creating a set of SOPs to define and guide the implementation of a 5S system encourages ongoing implementation and builds better habits, now and in the future. This cements 5S and transforms the effort from a project to a modus operandi.
Implementation of standardize is a systematic review of the actual actions that team members take in implementing sort, straighten, and shine. The required actions are:
- Document every area and every action.
- Review and document in teams of two, so one person walks through the tasks as another captures the details.
- Memorialize the essence; keep it simple and short, without missing critical steps. This way, there’s more chance that it will be maintained and used. Overdoing the recording is too often one of those “some stupid supervisor said so” events.
- Use short checklists that are more likely to be used. The live document at the workplace can be simply a series of keywords. The deeper detail can be kept for upskilling new staff as a training aid.
- Orderly simplicity will help. Organize the checklists by task/area, by shift, and by frequency. This will make the 5S process much less daunting to the team.
Creating standardized checklists can be a powerful review tool to assess whether they add value, what value the processes have already added, and what gaps may remain. Good examples of standardized look like this:
- List the team's 5S practices from an overview perspective.
- Recognize the need for both implementation and audit checklists, but never let the audit checklist get ahead of the implementation checklist.
- Prepare handbooks or kits with the materials needed for each area and task type.
- Keep the training materials live, with photos and effective visuals.
- Build a schedule for tasks, audits, and reviews, and make it practical rather than an excessive burden.
Step 5. Shitsuke (躾)/Sustain
Sustain is less of a step and more of a mindset. It ensures that 5S keeps being applied and remains a living and evolving part of the team ethos. When you sustain, you know that your work in standardized was productive and effective. A key plank in sustainability is to celebrate the improvements, sharing data, anecdotes, client reviews, and revenue outcomes.
The need to sustain is obvious, because otherwise all the effort of sort, straighten, shine, and standardize was wasted. And iteration of the first four of the 5S processes is the key to making them stick. Implementing sustain is where many companies struggle. The only way is to continually act out the standardize stage and evolve your approach, increasing the empowerment of the team as their engagement increases. The required actions for sustain are:
- Schedule. Build 5S practices into scheduled tasks across the whole team. Remember to find the wins and celebrate them.
- Lead by example, teach by demonstration. This will prepare staff to want to act on their own, for the team's benefit.
- Evolve people from supervised to solo status as fast as they move, not on a preordained schedule. It is easy to make mistakes, so patiently and helpfully offer support.
- Adapt and be agile. Give and receive feedback with kindness, grace, and a wider vision. Attack and defense are counterproductive.
- Agree on where changes can be made to make the tasks easier and more efficient.
The heart of 5S is agile, continuous improvement, which can only come from continuous and open feedback. Seek ideas and solicit opinions, and approach every such moment with curiosity and a genuine desire to learn. Some clear examples of sustain moments are:
- Hold short demo sessions to explain more complex processes to anyone who needs to know, and anyone who wants to know.
- Take note of the complainant and the enthusiast, and build up the latter to encourage the former.
- Keep training as an every-moment, opportunistic presence.
- Empower the team to run 5S audits for each other.
- Treat mistakes as reveals, rather than failures.
- Encourage everyone to communicate openly and constructively; never let the blame be the outcome, but find ways to improve your operation.
- Review the red-tag holding area regularly; don't let that become the proxy mess.
Like all new programs, implementing 5S in your shops may be a struggle at first. But doing it consistently will make it a lot easier in the long run and will offer many benefits for your organization.
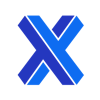