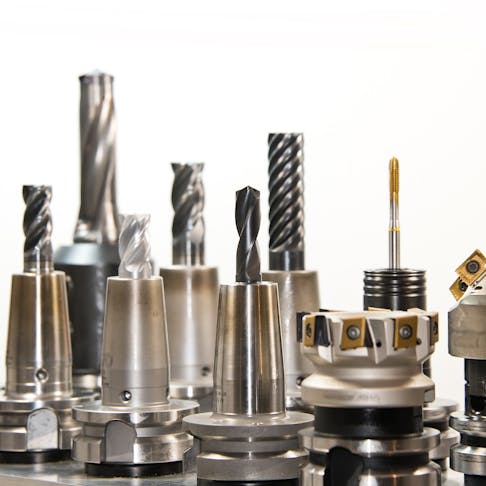
8 Ways to Extend Tool Life
Extending tool life can be beneficial for manufacturers in terms of cost and profitability. Learn how you can do it too.
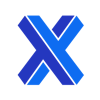
Tool wear is a normal part of the machining process. It’s inevitable that tools will fail, and that you’ll need to stop machines to change out old tools for new ones. But if you wait too long, and the tool fails in operation, you may end up having to scrap a damaged workpiece as well as a broken tool. In this article, we will look at ways to extend tool life, and improve your machining operations—and your profitability.
Why Extend Tool Life?
Finding ways to extend the life of your machine tools can be a key contributor to the profitability of your manufacturing operation by reducing tool replacement costs and minimizing downtime. Catastrophic tool failures can destroy the expensive product, as well as pose a risk of jamming up automated loading and conveyor equipment. Therefore, a careful study of how to extend tool life will pay dividends in lower costs, better uptime, and less scrap. Protecting your tools protects your profits.
Tips for Extending Tool Life
Not every suggestion will fit every fabrication process. Start with the tips that will have the biggest payoff for your business. Below are eight ways that you can extend the life of your manufacturing tools:
1. Plan feeds and Speeds Carefully
Cutting speed and feed rate are important parameters for the sustainable success of your manufacturing. Although it is tempting to set these rates as high as possible, this may not be the wisest approach in the long run. Go back to basics to calculate the feeds and speeds directly from the tool supplier’s recommendation. The rigidity and specification of the tool will dictate what is possible. The material of the workpiece is a key factor in choosing your feeds and speeds, as is the type of machining you’re performing (roughing or finishing).
With this tool supplier’s suggestion as the starting point, use your experience with the material (and similar projects) to adjust a little faster or slower to give the right quality of finish without overloading the tool.
2. Use the Correct Cutting Fluid
Heat generation in the tool is inevitable in machining but needs to be limited to extend the tool’s life. Excessive heat is a major factor in tool wear and breakage. Heat generation is more significant during roughing rather than finishing, due to the much higher material removal rate in roughing. The heat can be managed by using high-efficiency milling (HEM), where a large axial DOC allows wider distribution of heat in the tool. Compensating for chip thinning also maximizes the heat removed in the evacuated chips. Cutting fluid is another weapon in the arsenal for removing heat during cutting, by acting as a coolant and absorbing heat from the tool and the workpiece. Cutting fluid does more than that though — it also helps to evacuate chips more effectively and provides some lubrication.
3. Ensure Chips Are Evacuated
A sure way to shorten the life of your tool is to allow chip build-up as it causes additional flank and crater wear. Once formed, chips must be fully evacuated. Chips are also the primary means of heat removal from the cutting interface, so they must be cleared immediately to control the temperature of the tool. If a cutting fluid is not being used, but you are dry machining, compressed air can be directed near the tool’s cutting face to clear chips.
4. Consider the Wear Over the Full Tool
When looking to optimize the life of a tool, aim to distribute the wear evenly over the cutting edge of the tool. This includes taking flank wear into account when choosing settings and speeds. High-efficiency milling (HEM) achieves this by utilizing a large axial depth of cut, thereby engaging most of the cutting edge of the tool. This allows the heat and the wear to be distributed over a larger area. Keeping the heat evenly along the tool helps to reduce the likelihood of thermal cracking, which in turn would lead to chipping and potential failure of the tool.
5. Optimize the Depth of Cut Per Tool Pass
Although it can be tempting to maximize the depth of cut (or similarly, the stepover), taking a calculated approach to set the depth of cut can extend your tool life. Consider both the axial and radial depth of cut (DOC). Typical milling assumes a relatively heavy radial depth of cut, with a limited axial depth of cut. This radial DOC can be as much as 30-50% for roughing, but much smaller for finishing (3-5%). The axial DOC should then be adjusted according to the calculated load allowed on the tool. If you are noticing chatter or visual deflection of the tool, it would be wise to reduce the depth of the cut in order to extend the tool's life.
6. Reduce Tool Runout
The runout of a tool is essentially how far off its true axis a tool moves while rotating. Runout cannot be avoided entirely but must be limited as far as possible, to within an acceptable tolerance for the size of the tool. Excessive runout not only affects the tool life but also affects the accuracy and precision of the cut leading to scrapping parts. To improve runout, use high-quality tools that are straight and rigid, ideally with a maximum runout allowance of 0.0002” or less. Also, use precision tool holders with mechanisms that apply even pressure on the full circumference of the tool’s shank, such as shrink-fit and press-fit tool holders.
7. Reduce Tool Runout
To optimize your machining operation, consider whether a specialized cutting tool could be helpful. Rather than applying a general-purpose tool to every job, match the tool grade to the needs of the job. Although it can be a hassle to keep additional tool specifications on hand, in key jobs, it will pay itself back by extending the tool life.
8. Update Your Tool Path Planning Software
Getting the most out of your tools relies on carefully programming the optimum toolpaths. Check your existing CNC control software if it is still updated. If not, look for better CNC control software and make sure that your programmer is fully trained on the capabilities of the software to help maximize tool life. As a start, trochoidal toolpaths take advantage of chip-thinning to generate less heat and preserve the life of the tool. The tool can also be programmed to arc in and out of a cut.
Extending Tool Life - A Win-Win Situation
Making the effort to extend tool life in your machine shop will pay off in the long run by increasing the profitability of your operation. It will also reduce the hassle of stopping the machine and having to change out yet another prematurely failed tool and maybe scrap the workpiece, too.
The eight tips above can help you drive improvements in your workshop. Small changes can push your machining capabilities (and your business) closer to peak performance.
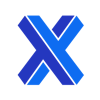