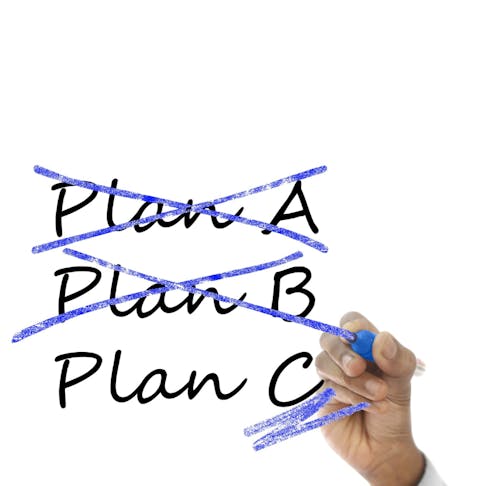
Steps in Developing a Workforce Contingency Plan for Manufacturers
A workforce contingency plan helps manufacturers maintain operations in the event of a disruption such as a calamity, pandemic, or personnel shortage.
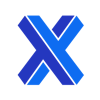
Disruptions to the workforce can have a ripple effect that may severely impact a company's ability to continue operating. That's why having a workforce contingency plan is essential for manufacturers. As the workforce becomes increasingly mobile and globalized, the need for contingency planning becomes necessary.
Many companies are now turning to workforce contingency planning to mitigate the risk of disruptions and ensure the continuity of operations. Whether it's a natural disaster, a pandemic, or a workforce strike, manufacturers need to be prepared for any eventuality.
So, what exactly is workforce contingency planning? And what steps should manufacturers take to develop a plan that will work for them? In this article, we'll explore the answers to these questions and more.
What Is Workforce Contingency Planning?
Workforce contingency planning is the process of creating a plan to ensure that critical workforce functions can be maintained in the event of an interruption. The goal is to minimize the impact of disruptions and maintain business continuity. Many potential disruptions could impact the workforce, including natural disasters, pandemics, workforce strikes, and terrorist attacks.
While workforce contingency planning is essential for all businesses, it is particularly critical for manufacturers. That's because interfering with the manufacturing process can have a domino effect that can quickly lead to production delays and other disruptions. For example, if a key supplier is unable to deliver raw materials due to a natural disaster, it could impact the manufacturing process and lead to production delays. Or, the failure of a critical piece of equipment could bring production to a standstill. In either case, having a workforce contingency plan in place can help to mitigate the impact of disruptions and ensure that operations can continue with minimal hiccups.
Elements of a Workforce Contingency Plan
Every workforce contingency plan is different, but some key elements should be included in all plans. These elements include:
1. Protection
The priority of any workforce contingency plan is to protect the organization's resources, including its workforce. The plan should identify which workforce functions are critical to the operation of the business and establish protocols for safeguarding these functions in the event of a disruption.
2. Detection
Whether it's a natural disaster or a workforce strike, it's important to have systems in place to quickly detect disruptions as early as possible. The contingency plan should identify the warning signs of a potential disruption and establish procedures for monitoring these signs.
3. Recoverability
Once a disruption has been detected, the contingency plan should outline the steps that need to be taken to recover from the event. This may include steps such as activating the plan, notifying employees, and mobilizing resources.
4. Resiliency
The final goal of any workforce contingency plan is to ensure that the organization can bounce back from any interruption and resume operations as quickly as possible. The plan should identify the resources that will be needed to recover from the event and establish procedures for accessing these resources.
Steps to Developing a Workforce Contingency Plan
1. Assess the Risks
The first step in workforce contingency planning is to assess the risks that could impact the business. This includes identifying which workforce functions are critical to the operation of the business and assessing the likelihood of disruptions to these functions. Many businesses use a risk matrix to identify and assess risks. A risk matrix is a tool that helps to visualize the risks that could impact the business and prioritize them based on the likelihood and severity of the potential consequences.
Internal and external factors should be considered when assessing risks, as both can impact the workforce. For example, an external factor such as a pandemic could cause an increase in absenteeism, while an internal factor such as workforce morale could lead to a decrease in productivity. Once the risks have been identified and assessed, the next step is to develop strategies for mitigating these risks.
2. Develop Mitigation Strategies
There are a variety of mitigation strategies that can be used to reduce the impact of workforce disruptions. Some common strategies include:
- Cross-Training Employees: Cross-training employees helps to ensure that critical workforce functions can be performed even if key personnel are unavailable.
- Building a Talent Pool: A talent pool is a group of pre-screened and qualified candidates that can be called upon to fill critical workforce positions in the event of a disruption.
- Implementing Workforce Tracking Systems: Workforce tracking systems can help to identify workforce shortages and schedule employees accordingly.
- Creating Work-From-Home Policies: Work-from-home policies allow employees to continue working even if they are unable to come into the office.
- Developing Communication Plans: Communication plans help to ensure that employees are kept up to date on the latest information in the event of a workforce disruption.
These are just a few of the many strategies that can be used to mitigate workforce disruptions. The best mitigation strategy will vary depending on the specific risks faced by the organization.
3. Implementation—Cascading the Workforce Contingency Plan
Once the workforce contingency plan has been developed, it's important to ensure all employees are aware of the plan and know what their roles are in the event of a disruption. The plan should be cascaded down through the organization. In some cases, it may be necessary to provide training on the workforce contingency plan.
This is especially true for critical positions that require specialized skills. It's also important to regularly review and update the workforce contingency plan. The plan should be reviewed at least annually and updated as needed to reflect changes in the workforce or the organization's risks. Developing a workforce contingency plan is an important part of managing workforce risk. By taking the time to assess the risks faced by the organization and develop mitigation strategies, businesses can minimize the impact of workforce disruptions and keep their operations running smoothly.
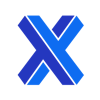