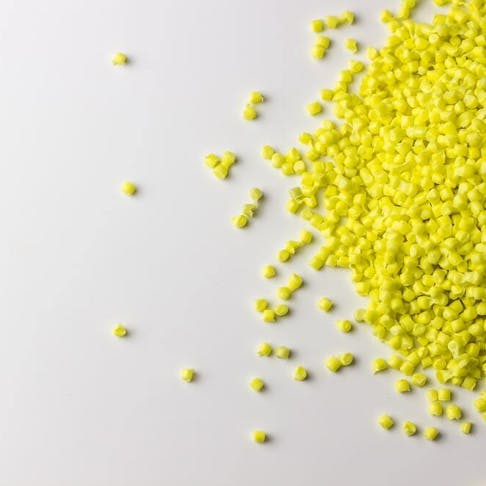
Thermoplastic Elastomers (TPEs)
Learn all about this material and its types, uses, advantages, and toxicity.
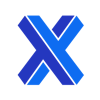
Thermoplastic elastomers (TPEs), also known as thermoplastic rubber, are materials that have the properties of thermoplastics. They also have the flexibility and elasticity of materials like rubber and polyurethane. These properties make TPE ideal for applications that require both mechanical strength and flexibility. TPEs can be melt-processed using standard thermoplastics equipment.
This article will describe what TPEs are, how they are made, the typical grades, and the advantages/disadvantages of using the material. The image below is an example of a shoe sole made with TPE:
Black soles made of thermoplastic elastomer.
Image Credit: Jemva/Shutterstock.com
What Are Thermoplastic Elastomers (TPEs)?
A thermoplastic elastomer (TPE) refers to any polymer that has elastic or rubber-like behavior. TPEs extend or compress when exposed to a load and will return to their original shape after the load is removed. Thermoplastic polymers can be formed using melt-processing techniques such as: injection molding, blow molding, or 3D printing. As the plastic cools down, it hardens and does not need to cure as is the case with thermosetting elastomers. Many TPEs can be melted and recycled. TPEs are therefore easy to process while retaining the properties common with thermosetting elastomers. Thermoplastic elastomers have a molecular structure made up of hard and soft segments as described below:
- Hard Segments: Typically crystalline in nature, these hard segments give the material its plastic-like behavior. These segments are responsible for properties like melting temperature, chemical resistance, and tensile strength.
- Soft Segments: Typically amorphous in nature, these segments give the material its elastomeric properties like flexibility, hardness, and permanent set.
The image below illustrates the hard and soft segments of TPEs:
Chemical composition of TPEs.
Image Credit: What is TPE?/elastomer.kuraray.com
How Are Thermoplastic Elastomers (TPEs) Made?
Thermoplastic elastomers are chemically synthesized using processes like graft or chain copolymerization. These work by copolymerizing two or more monomers. One of the monomers forms hard crystalline segments and the other will form into an amorphous or soft segment that gives the material its elastomeric nature. The two copolymerization techniques are described below:
- Block Copolymerization: This process creates a polymer backbone with repeating blocks of hard and soft segments.
- Graft Polymerization: This process grafts polymer chains as branches to a polymer backbone. This method allows for more customization as the branches and backbone can have a varying degree of hard and soft segments.
What Are the Types of Thermoplastic Elastomers (TPEs)?
There are many different grades of TPE material, however, listed below are the most commonly used types of TPE:
- Styrenic Block Copolymers (TPE-S): Used in footwear and seals and is one of the most widely used TPEs.
- Thermoplastic Polyolefins (TPO): Typically used in applications where standard polypropylene is not sufficient in terms of toughness.
- Thermoplastic Vulcanisates (TPV): A specially prepared mixture of EPDM (ethylene propylene diene monomer) and PP (polypropylene). This type of TPE has high-temperature resistance of up to 120C and is used for automotive seals.
- Thermoplastic Polyurethanes (TPU): This material has excellent abrasion and tear resistance and good rebound resilience.
- Thermoplastic Copolyesters (TPE-E): Has an excellent temperature resistance of up to 140C, one of the highest possible with TPE material. TPE-E also has excellent chemical resistance.
- Melt-Processable Rubber (MPR): Designed to replace nitrile rubber and as such has excellent resistance to oils and grease. MPR also shares other properties with standard rubber, like good stress relaxation properties and good rebound resilience.
- Thermoplastic Polyether Block Amides (TPE-A): Has good high-temperature resistance and can be bonded to polyamide (nylon) thermoplastics.
For more information, see our article on Types of Thermoplastic Elastomers.
What Are the Uses of Thermoplastic Elastomers (TPEs)?
TPEs are used in many different applications that can specifically benefit from their elastomeric properties. Some typical TPE products and their associated industries are listed below:
- Consumer Products: Blenders, cell phone covers
- Automotive: Seals, car mats, interior panels, airbag covers, shock dust boots
- Food & Beverage: Food containers, water bottles
- Medical: Flexible tubing, dental polishers, oxygen masks
- Industrial: Seals, bushes, vibration isolation mounts
- Sportswear: Helmets, swimming fins, snorkels, shoe soles
- Pet Products: Toys, feeding bowls, transport kennels
- Electronics: Cable insulation, plugs
- Power tools: Soft tool grips
For more information see our guide on the Uses of Thermoplastic Elastomers.
What Are the Advantages of Thermoplastic Elastomers (TPEs)?
Thermoplastic elastomers (TPEs) have the processability of thermoplastics and the flexible properties of elastomers. Listed below are some TPE material properties:
- Low-Energy Production: Thermoset and vulcanizing processes require high amounts of energy for manufacturing. TPEs, on the other hand, do not require the same amounts of energy, making them more energy-efficient.
- Recyclable: Like other thermoplastics, TPEs can be remelted and reused thereby making them recyclable
- Favorable Mechanical Properties: TPEs have many of the mechanical properties of high-performance elastomers. As such they have excellent flexural strength, good fatigue strength, and excellent abrasion resistance.
- Melt Processable: One of the main benefits of TPE is its suitability for typical melt-processing techniques like injection molding. This means that high-volume and low-cost parts can be made from materials that were historically only possible with expensive and complex thermosetting and vulcanizing processes.
- Easily Colored: Dyes and pigments readily affect TPEs. As such, they can be made into a wide array of colors.
For more information as our guide on Advantages of Thermoplastic Elastomers.
What Are the Disadvantages of Thermoplastic Elastomers (TPEs)?
Despite excellent thermoplastic elastomer properties, TPEs also have some key disadvantages as listed below:
- Hygroscopic: TPEs tend to absorb moisture and as such need to be sufficiently dried before processing.
- Melting: The TPE melting point is low, and as such TPEs are melt-processable using standard thermoplastic techniques. However, TPEs can be permanently damaged if heated past the degradation temperature of the soft segments in the polymer. This limits their high-temperature applications.
- High Hardness: TPEs are generally harder than other elastomers like rubber or polyurethane. This is in part due to the inclusion of thermoplastic hard segments within the polymer. Hardnesses are typically 80 Shore A and above.
How Do Thermoplastic Elastomers (TPEs) Affect Human Health?
Prolonged skin contact with TPE is not known to produce allergic dermatitis. TPE powder in the eyes, on the other hand, may cause mechanical irritation. Inhaling TPE powder may also irritate the respiratory tract. However, these risks are typically only present during the manufacturing of TPE parts. Normal use would not expose consumers to these hazards.
Are Thermoplastic Elastomers (TPEs) Toxic?
Thermoplastic elastomers are not toxic, and both food-safe and biocompatible grades are available. If combusted, TPEs can produce harmful combustion products that may be toxic such as hydrocarbons and formaldehyde.
Can Thermoplastic Elastomers Be Recycled?
Thermoplastic elastomers can be recycled as they can be melt-processed. This allows any unused TPE to be granulated and easily reused.
Summary
This article provided a look at Thermoplastic Elastomer materials, including the types, uses, applications, method of production, and toxicity. To learn more about the various thermoplastic elastomers applications and how best to use TPE material to meet your unique requirements, contact one of our application engineers or material specialists for assistance.
Disclaimer
The content appearing on this webpage is for informational purposes only. Xometry makes no representation or warranty of any kind, be it expressed or implied, as to the accuracy, completeness, or validity of the information. Any performance parameters, geometric tolerances, specific design features, quality and types of materials, or processes should not be inferred to represent what will be delivered by third-party suppliers or manufacturers through Xometry’s network. Buyers seeking quotes for parts are responsible for defining the specific requirements for those parts. Please refer to our terms and conditions for more information.
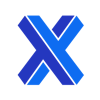