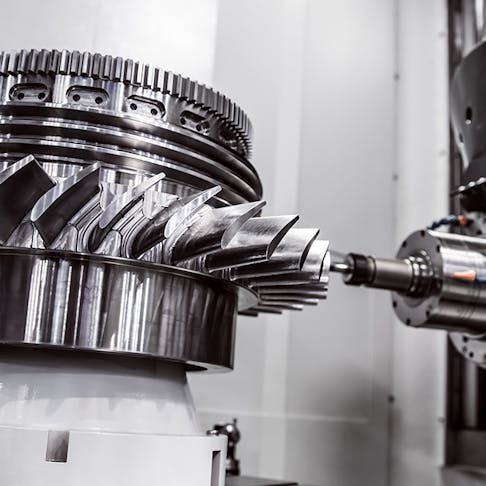
What is Nadcap Accreditation?
Nadcap accreditation is required for any company hoping to work with the biggest players in the global aerospace industry and is well worth the effort, improving the overall quality of a company's manufacturing processes.
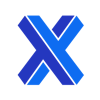
The aerospace industry is highly regulated due to the high levels of quality control required to assure maximum safety. It has a very low tolerance for failure due to the high stakes involved. One of the accreditation bodies introduced to improve and standardize quality control of aerospace manufacturing was Nadcap. This article will describe what Nadcap accreditation is and how to become accredited.
What is Nadcap?
Nadcap is an accreditation program that combines government stakeholders with industry experts to ensure compliance with a set of standards for the supplier approval process and is administered by the PRI (Performance Review Institute). The industry-managed nature of Nadcap means that government and industry work in tandem to create the requirements and issue accreditation to various aerospace suppliers. Before the creation of Nadcap, most aerospace companies would audit their suppliers to ensure they met a range of internal company standards. This led to duplicate audits and a large increase in workload for the suppliers.
However, most subcontractor failures could be traced to process and quality control problems in a select few special processes within the aerospace manufacturing industry. Nadcap prime subscribers formally identified these special processes, and a range of requirements and audits were implemented to ensure standardization across the industry and to eliminate duplicate audits. The audit criteria (AC) are adopted through industry consensus and are regularly reviewed and optimized. This ensures that compliance is more easily maintained since all major stakeholders agree on them.
The audits performed on these special processes are highly technical in nature. They are not merely a paperwork exercise, but rather enforce high standards for quality within the aerospace manufacturing industry.
Who Needs to be Accredited?
Any company that supplies components or services to aerospace OEMs who are subscribers of Nadcap, may be required to be audited. It depends on whether or not the supplier performs one of the special processes highlighted by Nadcap. The vast majority of major aerospace original equipment manufacturers (OEMs) are Nadcap members, including Airbus, Boeing, Rolls Royce, GE Aviation. If the company that performs these processes is not accredited, the prime subscriber will include Nadcap accreditation as a non-negotiable condition of further business dealings. A supplier can also proactively undertake the accreditation process without a prime subscriber’s specific request.
How Does the Auditing Process Work?
Whenever a prime subscriber engages a new supplier they must ensure that the supplier meets Nadcap’s special process audit requirements. A high-level flow chart of the Nadcap accreditation process is shown in Figure 1. The process begins with the OEM’s request that the supplier applies for Nadcap certification. The supplier will then need to contact Nadcap and request an auditor for their process, who is provided by the PRI. Typically a supplier will want to ensure that their relevant special processes comply with Nadcap’s requirements before the actual audit. The audit will then be scheduled and an auditor will be assigned by Nadcap. Once the audit has been completed, the auditor will report their findings and will highlight any non-conformances. This report will then be reviewed by the supplier and PRI technical staff who provide an additional support function to review the findings of the original auditor’s report. Any non-conformances must be addressed and closed out before the PRI technical staff issues the audit report to the prime subscriber. A task group at the OEM will then verify the conclusions of the report. At the end of this process, any additional Non-Conformances that may have been identified by the task group should be closed off and the supplier will be issued a certificate.
Figure 1: Nadcap Audit Flow Chart
The accreditation is not a one-off process and needs to be performed every 12 months. The renewal process is the same as the original audit and if standards were maintained from the last audit, the renewal audit will be less arduous. However, it's important to stay up to date with any changes that may have been made by Nadcap to ensure continued compliance.
How to Prepare for an Audit?
Nadcap makes the audit process very easy. They offer multiple sources of information relating to the process, some of which are listed below:
- Audit Check Sheets: All of the relevant audit check sheets and reference material are made available before the audit via the eAuditNet portal. A partial list of these special processes is shown in Table 1. Additional checklists relating to sub-processes may also be applicable.
- Pre-Assessment Audit: A pre-assessment audit can be requested to help the supplier identify any non-conformances that they may have missed in their internal preparation process.
- Training: Nadcap offers training that covers a range of topics, including root cause corrective action, how to prepare for an audit, and how to implement an efficient internal audit process.
If a company exports weapons, it needs to conform with ITAR (International Traffic in Arms Regulations). This fact needs to be communicated to Nadcap so that an auditor with the appropriate export status, i.e individuals who have the relevant clearance to audit companies who manufacture arms, is sent to conduct the Nadcap audit.
List of Nadcap Auditable Special Processes
Number | Special Process | Relevant Standard/Checklist |
---|---|---|
Number 1 | Special Process Aerospace Quality Systems Standard | Relevant Standard/Checklist AS/EN/JISQ9100, ISO 17025 |
Number 2 | Special Process Chemical Processing | Relevant Standard/Checklist AC7108 |
Number 3 | Special Process Coatings | Relevant Standard/Checklist AC7109 |
Number 4 | Special Process Composites | Relevant Standard/Checklist AC7118 |
Number 5 | Special Process Conventional Machining as a Special Process | Relevant Standard/Checklist AC7126 |
Number 6 | Special Process Elastomer Seals | Relevant Standard/Checklist AC7115 |
Number 7 | Special Process Electronics | Relevant Standard/Checklist AC7119, AC7120/AC7121 |
Number 8 | Special Process Fluid Distribution Systems | Relevant Standard/Checklist AC7112 |
Number 9 | Special Process Heat Treating | Relevant Standard/Checklist AC7102 |
Number 10 | Special Process Materials & Testing Laboratories | Relevant Standard/Checklist AC7101 |
Number 11 | Special Process Measurement & Inspection | Relevant Standard/Checklist AC7130 |
Number 12 | Special Process Non-Metallic Materials Testing | Relevant Standard/Checklist AC7122 |
Number 13 | Special Process Non-Metallic Materials Manufacturing | Relevant Standard/Checklist AC7124 |
Number 14 | Special Process Non-Destructive Testing | Relevant Standard/Checklist AC7114 |
Number 15 | Special Process Non-Conventional Machining & Surface Treatment | Relevant Standard/Checklist AC7116, AC7117 |
Number 16 | Special Process Sealants | Relevant Standard/Checklist AC7200/1, AC7202 |
Number 17 | Special Process Welding | Relevant Standard/Checklist AC7110 |
List of Nadcap auditable special processes with the corresponding standards from the eAuditNet portal.
What are the Benefits of Accreditation?
Nadcap accreditation is compulsory for a large number of major aerospace companies. Suppliers who maintain their Nadcap accreditations may find the bidding process with these companies easier. The OEM will not need to waste time helping to bring an unaccredited supplier into compliance. Nadcap accreditation proves that a company strictly follows industry-recognized best practices and in some cases, this has more weight than ISO 9001 accreditation, because Nadcap accreditation means that detailed audits of internal special processes were performed, and the supplier’s actual processes meet the required standards.
Nadcap certification is required for any company hoping to work with the biggest players in the global aerospace industry. Having this accreditation will allow these aerospace giants to have confidence that a supplier can perform within the stringent requirements of the industry at face value. This can help a company stand out above all those others that are not accredited, thus gaining a degree of international recognition within the aerospace industry. Nadcap accreditation has the added benefit of improving the overall quality of a company's manufacturing processes, thus reducing warranty costs. Quality is assured with Nadcap accredited companies and the aerospace industry is well aware of this, making this accreditation well worth the effort.
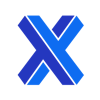