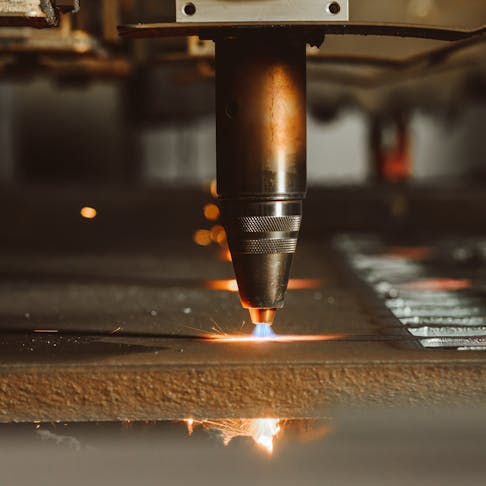
A Guide to Oxygen Fuel Cutting
Learn more about oxygen fuel cutting and how it works.
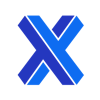
Oxygen is an abundant gas in nature. It makes up 21% of the air we breathe. Oxygen fuel cutting is the use of oxygen gas combined with other combustible gasses to melt and cut through steel. When pure oxygen is added to a flame of acetylene, propane, or other hydrocarbons, the flame temperature is greatly increased. This oxygen fuel effect can be used to heat, melt, and cut steel. The hydrocarbon gasses mixed with oxygen are often referred to as oxyfuels. This article will discuss oxygen fuel cutting, how it works, the types of equipment, and the industries and applications that use it.
What Is Oxygen Fuel Cutting
Oxygen fuel cutting is the use of combustible gasses mixed with oxygen to melt and cut steel. It is used to cut mild steel by initiating a chemical reaction within the material as it melts. The fuel gasses, mixed with oxygen, heat the steel to its ignition temperature using a flame from a torch. A blast of high-pressure oxygen is then blown onto the surface which forms iron oxide in reaction with the semi-molten steel. This material burns and is blown away by the oxygen flow. Figure 1 is an example of oxy-fuel cutting:
An example of oxy-fuel cutting with steel.
Image Credit: Shutterstock.com/A. Aleksandravicius
Thick steel sections can be cut quickly and easily using oxygen fuel cutting. It is used in steel fabrication, metal shops, construction, and nautical applications. There are several different gasses that can be used in combination with oxygen. Acetylene, propane, MAPP (methylacetylene-propadiene), and natural gas are the most common oxyfuels.
How Does Oxygen Fuel Cutting Work?
Oxygen fuel cutting works by igniting fuel and oxygen and bringing the flame into contact with the material to be cut. The hot temperature brings the material along the cut line to its “kindling” (or ignition) temperature, and it starts to glow red. For carbon steel, this temperature is 700 to 900°C. When a stream of oxygen is shot at the red-hot material, a chemical reaction occurs and iron oxide is formed. This molten material is then blown away by the high-pressure oxygen.
Several elements are needed to make a cut using oxygen fuel cutting, including:
- Oxygen: A gas bottle cylinder of pure oxygen is required. The most common oxygen purity level used for oxygen fuel cutting is 99.5%.
- Fuel Gas: Acetylene is the most commonly used fuel gas. It is normally stored in pressurized gas cylinders. Multiple cylinders can be stored and transported together on a trolley.
- Connection Pipes: The oxygen and fuel are connected to the cutting torch with separate pipes, and are generally mixed together at the outlet end of the torch.
- Cutting Torch: The torch is connected to the oxygen and fuel lines and is passed over the material to be cut. The flame is ignited at the tip of the torch.
- Gas Regulator Valves: A regulator is a valve that controls the flow of gas from the cylinders and the mixture of oxygen and fuel. Both the gas bottles and the torch have pressure regulator valves. These can be controlled manually or automatically, depending on the machine.
- Ignition: To start the flame at the tip of the torch, a controlled ignition source is needed. A flint lighter or electronic spark is often used to ignite the flame.
- Protective Equipment: Safety glasses such as: darkened glasses, goggles, or welding masks, must be worn when operating an oxyfuel torch. The flame produces high-intensity light which can cause permanent damage to your eyes. High-temperature gloves and protective clothing and footwear are also required when operating an oxygen fuel cutter.
What Oxygen Fuel Cutting Machine Is the Most Popular?
The most popular oxygen fuel-cutting machine are listed below:
- Acrbro: Arcbro manufactures a range of oxygen-cutting machines at different price points. At the entry-level, the Arcboy Scout 2 is an X-Y axis oxygen fuel cutter. This is an inexpensive system used mainly for straight-line cuts. The system is easy and quick to set up or mount but is not very versatile in terms of the shapes and contours it can cut. It can only be used on flat material.
- Kerf: The Kerf RUR Cutting Machine is a CNC-controlled oxygen fuel-cutting machine that operates in three axes (X, Y, and Z). With table sizes ranging from 1.5-5 m wide, this machine suits a wide range of applications, including: steel component production, tool making, and automotive components. The Kerf RUR combines oxyfuel and plasma-cutting functions in a single system. This makes the system suitable for thinner steel sections, as well as non-carbon steel materials. The RUR series is a popular system for small and medium workshops and factories.
- Zinser: Zinser manufactures a number of different types of steel-cutting machines. A common application for oxyfuel cutting is the machining of thick steel pipe and tubing. The Zinser 1304 Universal Pipe Cutter machine is designed for this specific application. The system can cut steel pipes of diameters from 50-500 mm. The pipe is clamped in position using a chuck and then rotated during the machining process. The stationary oxygen fuel torch cuts sections or cutouts while the pipe moves. This system is popular for construction, and structural component manufacture.
Manual oxygen fuel cutting (using a torch connected to oxygen and fuel tanks) is still widely used and is a popular method of cutting steel in metal fabrication shops, construction sites, and nautical applications. This is due to its portability and the ability to cut steel without the need for electricity.
What Distinguishes Oxygen Fuel Cutting From Other Forms of Cutting?
Oxygen fuel cutting is distinguished from other forms of cutting by its portability and its speed in cutting mild steel. It can cut steel plates up to 12 inches in thickness (compared to 2 inches for laser cutting and 3 inches for grinders). Plasma cutters are similar in performance to oxygen fuel cutters and are able to handle the same range of steel thicknesses. However, oxygen fuel cutting is about three times faster for thick plate material (2 inches and thicker).
It can be difficult to produce clean, straight cuts using oxygen fuel cutting, so this technique is often used where the appearance of the cut edge is not important. Oxyfuel cutters cut mild and low alloy steel very well, but they are limited to only these materials. Laser cutters, angle grinders, and plasma cutters can be used with many different types of steel, non-ferrous metals, and other materials.
What Is the Procedure for Cutting With Oxygen Fuel?
The procedure for cutting with oxygen fuel is given below:
- Setup: Fixture the workpiece in place with clamps or custom tooling. Wear appropriate personal protective equipment. Open the regulator valves at the oxygen and cutting fuel bottles. The gasses will then flow to the torch. Open the valves at the torch for the gasses to flow out of the torch tip. Ignite the flame using a flint lighter or an automatic electronic spark. Adjust the gas mixture to provide the shape and length of flame required for the application and material.
- Preheat: Heat the material to its kindling temperature and glow red before starting the cut. Increase the material's temperature close to its kindling temperature by passing the flame over the material along the cut line for a few seconds per inch.
- Piercing and Cutting: Hold the torch at the initial cutting point until the material begins to glow red. The gas jet will first pierce the material, and then cut it as the torch is moved along the intended cut line. While keeping the oxygen flow steady, move the torch slowly along the cut line, ensuring that the material has been cut all the way through. Ensure that there is clearance beneath the workpiece because of the molten iron oxide material which will drop from the cut edge.
- Finishing: When the cut is complete, switch off the gas valves at the torch. It is best practice to switch off the fuel gas first, followed by the oxygen. Then close the valves at the bottles. These valves may be under automatic control on CNC equipment. Any molten iron oxide (or “slag”) that remains on the cut edge can be tapped off with a hammer, or the edge can be evened out using an angle grinder.
What Kind of Gas Is Used in Oxygen Fuel Cutting?
The kind of gas used in oxygen fuel cutting depends on the material to be cut and its melting point. A fuel capable of generating a higher temperature is needed for cutting steel with higher melting points. Listed below are the three most commonly used gasses:
- Acetylene: Acetylene burns at a very high temperature compared with other oxyfuels. Its maximum flame temperature is 3,160°C. With such a high flame temperature, it most easily pierces the material for cutting.
- Propane: Propane’s maximum flame temperature is lower than that of acetylene, at 2,828°C. Because the flame temperature is lower, it takes more time to pierce the material to be cut. A propane torch can cut as fast as an acetylene torch, but it requires 3-4 times as much fuel to do so.
- MAPP: MAPP gas is a mixture of hydrocarbons, mostly methylacetylene and propadiene. Its maximum flame temperature is 2,976°C (lower than acetylene, but higher than propane). MAPP can be used at a higher pressure than acetylene, so it finds uses in underwater cutting and welding.
To What Industries Is the Oxygen Fuel Cutting Technique Applicable?
Oxygen fuel cutting is widely used in various industries and applications, including:
- Steel Fabrication: Many steel fabricators use oxygen fuel cutting because it is so versatile. It can be used for many cutting, welding, heating, and repair jobs commonly completed in steel workshops.
- Building and Construction: Cutting and adjustment of beams, steel channels, and steel base plates are usual uses for oxygen fuel cutters in the construction industry.
- Offshore Energy and Marine Applications: Oxygen cutting with MAPP gas can be performed at very high pressures, and is routinely used for steel cutting and repairs underwater on oil platforms and offshore energy rigs. Ship repair and other underwater applications regularly employ oxygen cutting.
What Types of Materials Are Appropriate for Oxygen Fuel Cutting?
Oxygen fuel cutting is suitable for steels with a carbon content of 0.04–0.3% (e.g., low-carbon and mild steel). For oxygen cutting to work, the melting point of the material must be lower than the temperature of the oxyacetylene on its own without the oxygen blast. Oxygen fuel cutting produces an exothermic (releases heat) chemical reaction at the cutting edge of the material, creating iron oxide, or “slag”. The slag is blown away by the high-pressure oxygen jet to create the cut. Materials that cannot be cut using the oxyfuel process include:
- Non-metals (for example, polymers and ceramics)
- Non-ferrous metals (for example, aluminum, copper, bronze)
- Stainless steel
- High-carbon steel
Is Cutting With Oxygen Fuel Quicker Than Other Types of Cutting?
Yes, oxygen fuel cutting is faster than plasma cutting, grinding, or laser cutting for thick sections of steel. Oxygen fuel cutting can cut 2-inch thick steel at a speed of around 12 inches per minute. This is around 3 times faster than plasma cutting. It is around half the speed of diamond-coated grinding discs (but some common angle grinders are limited to 3 inches in steel thickness). Laser and plasma cutting, however, is faster for thin sections of steel.
Is the Melting Speed of Oxygen Fuel Cutting Quick?
Yes, oxygen fuel cutting melts the workpiece very fast! It can pierce through steel in around 10 seconds. The piercing time is the time that the torch is in contact with the surface of the material before it pierces through. Oxygen fuel cutting can cut 2-inch-thick steel at a speed of around 12 inches per minute. The material must reach the kindling temperature (below its melting temperature, but glowing red hot) before you can start cutting. It is best practice to preheat along the cut line for a few seconds to bring the material close to its ignition temperature before pressing the oxygen switch and beginning to cut. Preheating the cut reduces piercing times from 20-120 seconds to under 10 seconds (depending on the thickness of the steel).
Is the Melting Cut in Oxygen Fuel Cutting High Quality?
No, the cut edges produced by oxygen fuel cutting are not of high quality. Cutting steel using oxygen fuel cutting is a very rapid process, but it does not produce a very clean cut. Oxygen fuel cutting uses oxygen to melt and burn the steel which starts a chemical reaction. The burning steel creates molten iron oxide which is blown away by the oxygen gas. Iron oxide (also known as “slag”) forms a distinctive pattern on the jagged cut edge. The quality of the cut can be improved by preheating the cut line to improve piercing, using a guide clamped in place along the cut line, and reducing cutting speed. Many cuts are finished using a grinder to clean off any slag and to straighten the cut line.
Oxyfuel cutting can cut thin steel, but below a thickness of 20 mm, the material tends to warp unless carefully preheated. Other cutting methods are generally used on thin steel plates, such as laser or plasma cutting, to create higher-quality finishes.
Summary
This article presented oxy-fuel cutting, explained what it is, and discussed how it works and the applications of this cutting method. To learn more about oxygen fuel cutting, contact a Xometry representative.
Xometry provides a wide range of manufacturing capabilities, including sheet cutting and other value-added services for all of your prototyping and production needs. Visit our website to learn more or to request a free, no-obligation quote.
Disclaimer
The content appearing on this webpage is for informational purposes only. Xometry makes no representation or warranty of any kind, be it expressed or implied, as to the accuracy, completeness, or validity of the information. Any performance parameters, geometric tolerances, specific design features, quality and types of materials, or processes should not be inferred to represent what will be delivered by third-party suppliers or manufacturers through Xometry’s network. Buyers seeking quotes for parts are responsible for defining the specific requirements for those parts. Please refer to our terms and conditions for more information.
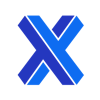