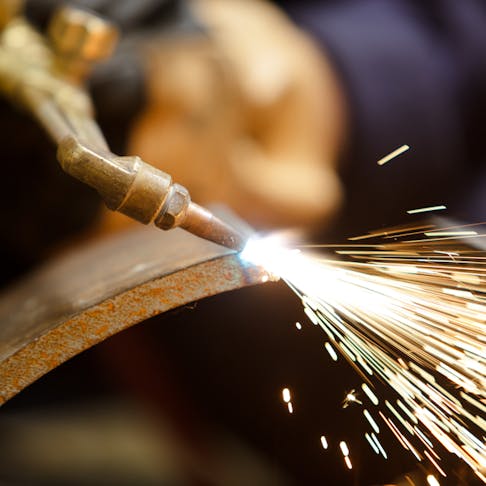
Gas Welding: Definition, Types, Applications, and Advantages
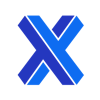
Gas welding is the process of joining two metal items together by melting and cooling parts of both. This is achieved by creating a very hot flame using oxygen and a fuel gas. There are a few main types of gas welding that use different gasses such as: acetylene, gasoline, MAPP (methylacetylene-propadiene propane), butane, propane, or hydrogen. Gas welding has been overtaken by electrical forms of welding in many applications. However, the portability, effectiveness, and simplicity of gas welding mean it still sees widespread use in most manufacturing industries.
What Is Gas Welding
Gas welding is a process that requires burning a gas fuel (usually acetylene) with oxygen to create enough heat to partially melt metal items and join them together. Gas welding is one of the most common forms of welding and is what many people instinctively picture when they think of welding.
What Is the Other Term for Gas Welding?
Gas welding is a general term that covers a few subcategories of welding. Acetylene welding is another term used interchangeably with gas welding because acetylene is the most common welding fuel. Specific types of gas welding include: oxy-acetylene, oxy-gasoline, MAPP, butane, propane, or hydrogen gas welding.
What Is the Importance of Gas Welding?
Gas welding is important in the fabrication of metal products. It’s a simple, mobile, and economical method for joining metal parts.
What Is the Purpose of Gas Welding?
The purpose of gas welding is to fuse ferrous or nonferrous metal items together and may be used instead of other fastening techniques. Manufacturers may choose gas welding over other forms of welding because it’s cheap and the equipment is portable.
How Does a Gas Welding Work?
Gas welding works by feeding both oxygen and fuel gas out of the end of a torch to produce a highly concentrated flame that can melt metal. Material is melted at the seam between two parts to create what is known as a weld pool. The pool then cools and bonds the pieces together to form a strong joint. The welder’s flame must be moved slowly to allow the joint to cool without oxidation which can create brittle connections.
What Are the Key Parameters of Gas Welding?
There are certain parameters which when altered will have an effect on the weld being produced. Most welders use acetylene as fuel, so gas welding is often referred to as oxy-acetylene welding. However, hydrogen, propylene, and butane are also options. The fuel type will have an effect on the four main parameters of the welding process:
- Temperature: The temperature of the gas welding flame is controlled by the oxygen-to-fuel ratio. More fuel means a lower temperature while less means a higher temperature. Different materials demand different temperatures based on their melting points.
- Pressure: By adjusting the pressure ratio between the delivery of oxygen and the fuel gas, different flames can be obtained. Three distinct flames are possible: neutral, oxidizing, and carburizing. The neutral flame is the most common and is identifiable by its small bright white inner flame and larger blue flame. It is made by mixing near-equal amounts of oxygen and fuel gas. An oxidizing flame is created by mixing more oxygen than fuel gas. Its inner flame is much shorter and more pointed than the neutral flame and burns slightly hotter. Oxidizing flames are important for welding cast iron, brass, bronze, and zinc alloys. The carburizing flame, by contrast, is created by mixing more fuel gas than oxygen and is identifiable by a visible secondary flame between the short inner flame and the larger envelope flame. The carburizing flame is used for aluminum and aluminum alloys.
- Speed: The speed at which a proper weld move is dictated by the time it takes to properly form a weld pool. The welder must be careful not to move so fast that the weld fails to complete, but must also not linger so long that they burn a hole through the metal.
- Gun Position: The gun position and feed rate of the filler metal will determine the weld pool size. A weld pool that grows too large indicates that it has received too much heat, so the operator must move the gun parallel to the weld to deflect heat. Conversely, if the weld pool is too small, it is too cold and therefore the welder must position the gun nearly perpendicular to the weld. Additionally, more filler material necessitates more heat, so if the weld pool is too hot the welder can add filler material faster and vice versa.
What Are the Different Types of Gas Welding?
There are five main different types of gas welding. They differ by the fuel gas involved:
- Butane or propane welding
- Hydrogen gas welding
- MAPP gas welding
- Oxy-acetylene gas welding
- Oxy-gasoline gas welding
What Are the Applications or Uses of Gas Welding?
One of the primary uses of gas welding services is repair work. This technique is better than most at bridging gaps between parts. Other applications of gas welding include:
- Fabrication of sheet metal
- Joining of aircraft parts
- Automotive chassis and frame fabrication
- Joining of high-carbon steel
How Does Gas Welding Being Utilized in Aerospace Industry?
Gas welding was the primary welding technique used in aerospace up until the mid-1950s when arc welding became widespread. However, gas welding is still used for the fabrication and repair of aircraft structures.
How To Use a Gas Welder?
The process of using a gas welder is listed below:
- Check if the setup is safe and secure. Ensure that the torch, hoses, regulators, and cylinders are attached correctly, and check that the nozzle is clear.
- Adjust the fuel gas with the nozzle’s regulator closed. Open the cylinder shut-off valve, and then slowly open the regulator to the right pressure. Once the right pressure is achieved, close the fuel gas shut-off valve at the torch.
- Repeat step two with the oxygen supply.
- Turn on only the fuel gas at the torch and ignite the flame. The flame will let off black smoke from unburnt carbon, so be careful not to inhale it. Open the fuel valve at the torch until the smoke has stopped.
- Open the oxygen valve at the torch and adjust it until you have the neutral, oxidizing, or carburizing flame that you need.
- Make sure the metal to be welded is correctly positioned on a heat-resistant material such as fire bricks.
- Before fully welding, place a tack weld at each end of the joint to prevent the pieces from moving during the process. To do this, hold the torch at a 45-degree angle close to the metal and move in a zigzag pattern between the metals, heating them until a weld pool forms. Once a weld pool forms, remove the heat.
- To weld the joint, create a weld pool by zigzagging the flame at a 45-degree angle across the two pieces of metal until a melted pool starts to form. Push the pool along by slowly moving the torch from one end to the other.
- Once the weld is complete, leave the metal to air-cool. Do not use water as this will make the weld brittle.
- When turning off the welding equipment, always turn off the fuel gas first and then the oxygen. If there is no more welding to be done, make sure to close the shut-off valves at the cylinders.
What Are Tips and Strategies To Have a High-Quality Gas Welding Result?
Here are a few tips to improve your gas welding technique:
- Use a zigzag or circular motion to evenly heat both metal items.
- Hold the torch at a 45-degree angle to the weld, then tilt it as needed to increase or decrease the impinging heat.
- Hold the torch 2-3 mm away from the weld site.
- The bigger the weld pool, the better the weld penetration. Be careful not to let the weld pool get large enough to create a hole.
- Small explosions at the nozzle signify that either the torch is too hot, it’s not getting enough fuel gas, or the nozzle needs to be cleaned.
Is Gas Welding Hard?
No, gas welding is one of the easier forms of welding. Beginners are often required to master gas welding before moving on to electrical methods.
Is Gas Welding for Beginners?
Yes, gas welding is good for beginner welders, although metal inert gas (MIG) and tungsten inert gas (TIG) may be easier for beginners.
What Are the Materials That Can Be Used in Gas Welding?
Most metal items can be gas welded to metals of the same composition. For example, steel can be welded to steel. However, aluminum cannot be welded to steel. Below are some examples of metals that are commonly gas welded:
1. Aluminum
Aluminum has a relatively low melting point of 1,220 degrees Fahrenheit and is welded using a carburizing flame. This type of flame is cooler than neutral and oxidizing flames. One important step that’s unique to aluminum is the removal of the oxide layer. This is because the oxide layer has a much higher melting point than the aluminum itself; if you melt the oxide layer, you risk quickly melting all the way through the metal below as well. Instead, the oxide layer must be removed using a brush.
2. Copper
Copper is used extensively to make pipes for water and gas supplies. Connections between copper pipes are usually either gas welded or formed using compression joints. Copper piping requires a different style of welding than other metals. To weld a copper pipe, a fitting is first placed over the pipe. Both the fitting and the pipe are then heated, but the heat is not applied directly to the joint area. Filler metal is then added to the joint and capillary action sucks the melt into the joint.
3. Stainless Steel
Stainless steel is an iron-based alloy containing at least 11% chromium. The chromium protects the steel from corrosion. Gas welding stainless steel is difficult because it has a higher melting point than regular steel, so it requires a lot of heat.
4. Brass
Brass is an alloy of copper and zinc and has a melting point of 1,710 °F. It is welded using an oxidizing flame. Brass is also highly thermally conductive, so only a large nozzle will be able to apply enough heat to melt the metal.
5. Cast Iron
Cast iron is an iron-based metal that contains more carbon than steel. It has a high melting point, so it needs an oxidizing flame. The hefty carbon content makes cast iron difficult to weld without creating cracks or problematic hard spots.
6. Nickel Alloys
Nickel-based alloys can be welded without significantly affecting their corrosion resistance or mechanical properties. Nickel alloys are formed mostly of nickel with varying amounts of chromium and molybdenum. Nickel alloys should not be welded using oxy-acetylene welding. TIG welding or MIG welding should be used instead.
What Are the Materials That Cannot Be Use in Gas Welding?
Nonmetals, including composites, woods, and plastics, cannot be gas welded. And even weldable metals have limitations. Dissimilar metals typically cannot be gas welded to one another. For example, aluminum and steel, aluminum and copper, or titanium and steel melt at significantly different temperatures, so they can’t form a proper weld pool together.
How Durable Is a Gas Weld?
A good weld can be as strong as the metal parts it joins. However, that assumes it fully penetrates the joint. If the joined parts butt too closely together or are simply too thick, the weld may not complete properly. Gas welds also need to be air-cooled to be strong. If quenched in water or other fluids, the weld will become brittle.
How Much Does Gas Welding Machine Cost?
Welding machines are relatively cheap but vary in quality. Basic DIY systems go for approximately $300 while high-end ones can range all the way up to approximately $5000.
How Long Does a Gas Welding Machine Last?
Most welding machines will easily last 10 years with regular use. If regularly maintained, though, they should survive 20 years or more.
What Are the Advantages of Gas Welding?
Gas welding has many advantages, the most notable of which is its low cost. Other advantages of this technology are:
- It can join parts made of both ferrous and non-ferrous metals.
- It does not require electricity which means it can be used in isolated areas.
- It does not require high-rated skills.
- Welding equipment is portable, requiring only a fuel and oxygen tank, control valves, and a torch.
What Are the Disadvantages of Gas Welding?
The main disadvantage of gas welding versus other forms is that it is limited to relatively thin sections of metal. Other disadvantages of gas welding are:
- It usually requires post-processing if aesthetics are important.
- The heat affects the mechanical properties of high-strength steel.
- It is slower than other methods because it doesn’t get as hot.
- Its lack of flux shielding can cause weld defects.
What Are the Side-Effects of Gas Welding?
Gas welding is a hazardous activity by nature and can cause harmful side effects. One of the most prominent is a respiratory illness. Welding can lead to asphyxiation when performed in a confined space. Other possible health side effects are:
- Skin burns
- Eye burns
- Coughing/occupational asthma
- Tight breathing
- Dizziness
- Fatigue
Is Gas Welding Hot Enough To Twist and Warp Metal?
Yes, gas welding can warp and twist metal. Metals such as copper and aluminum can warp when too much heat is added during welding. More specifically, warping occurs where there is rapid (and thus uneven) heating and cooling of the welded metal.
Can Gas Welding Take Longer Than Laser Welding?
Yes, gas welding takes longer than laser welding. Gas welding is limited by the heat at which the gasses burn. Laser welders can reach 200 inches per minute whereas gas welding is far slower.
What Is the Difference Between Gas Welding and Arc Welding?
The difference between gas welding and arc welding is that the former heats metal by burning gas while the latter creates heat through an arc of electricity. This makes gas welders portable but also arguably more dangerous. For more information, see our guide on Arc Welding vs. Gas Welding.
Summary
This article presented gas welding, explained it, and discussed its various types and applications. To learn more about gas welding, contact a Xometry representative.
Xometry provides a wide range of manufacturing capabilities, including sheet cutting and other value-added services for all of your prototyping and production needs. Visit our website to learn more or to request a free, no-obligation quote.
Disclaimer
The content appearing on this webpage is for informational purposes only. Xometry makes no representation or warranty of any kind, be it expressed or implied, as to the accuracy, completeness, or validity of the information. Any performance parameters, geometric tolerances, specific design features, quality and types of materials, or processes should not be inferred to represent what will be delivered by third-party suppliers or manufacturers through Xometry’s network. Buyers seeking quotes for parts are responsible for defining the specific requirements for those parts. Please refer to our terms and conditions for more information.
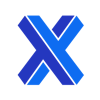