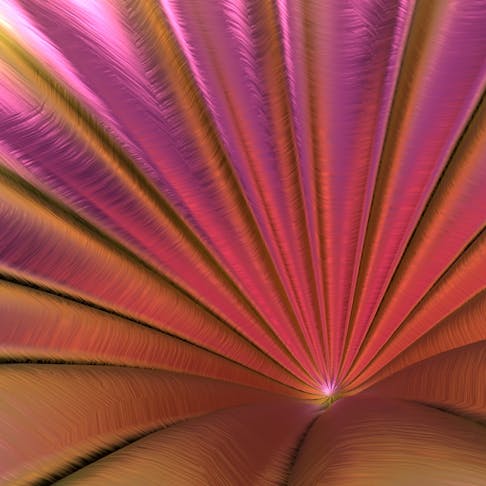
What Is the 720 Rule for Anodization?
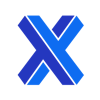
Anodization is a process through which the entire surface of a material (usually aluminum or titanium) is chemically reacted (oxidized) to form a protective and corrosion-resistant layer. This layer can also be colored for aesthetic effect. Figure 1 below shows some variations in coloration in anodized aluminum:
Anodized aluminum wheel rims.
Image Credit: Shutterstock.com/gualtiero boffi
The 720 rule for anodization is a simple calculation that helps you estimate how much time it will take for your aluminum part to form an anodized layer of the thickness you desire. The 720 rule makes the process of aluminum anodization predictable, which brings a number of other benefits. It does not, however, apply to other metals.
How Is the 720 Rule Implemented for Anodizing?
The 720 rule is an equation involving electric current, time, and desired anodic layer thickness. You can employ it by inputting known values and solving for the unknown variable. For instance, if you want to know how long a current needs to be applied to your part to form a 1.2-mil anodized layer, plug in that thickness and the electrical current density for your part and solve for time.
To anodize aluminum, the part is submerged in an acidic electrolyte solution and suspended from a conductive rack. Electrodes (cathodes) are also submerged in the bath. A voltage is applied, causing electrons to flow from the aluminum part (acting as the anode), through the electrolyte solution, and to the cathodes. In this way, the movement of electrons oxidizes aluminum atoms on the surface of the part. This causes an anodized layer to form and expand.
The 720 rule only applies to constant-current anodization. The current only remains constant if the voltage across the circuit increases to match the pace of anodized film growth. This ensures a constant current density (current per unit surface area of the aluminum component), which then ensures a constant rate of film growth. If done right, the anodized film’s thickness will be directly proportional to the length of time the anodization is carried out.
With a known and constant current density, the time required to achieve a specific anodized thickness can be estimated to an acceptable level of accuracy.
What Are the Benefits of the 720 Rule for Anodizing?
The 720 rule is a useful estimation. Most critically, it helps you predict the final anodized film thickness. Once you have an accurate time estimate, you can generate consistent results, so it helps you maintain quality control as well.
Another benefit of using the 720 rule for anodizing is that it speeds up the overall process. Since the thickness is predictable based purely on time, there is no need to interrupt the process to measure, and no trial-and-error approach. On large volumes, time savings on each part can translate into efficiency and financial savings.
What Is the Formula for the 720 Rule for Anodizing?
The formula for the 720 rule is shown below:
720 (Amps * minutes / ft^2 * mil) = current density x time / thickness
The product of the current density (in units of A/ft2) and the time of anodization (in minutes), divided by the thickness of the anodized film (in mils) will equal 720 (a unitless constant). The unit of a mil used for thickness is one-thousandth of an inch — 1 mil is 0.001” or 25.4µm.
Written in a different way to calculate time, the formula is as follows:
time (minutes) = 720 * thickness / current density
This formula represents the time required to generate a specific thickness of anodizing film (so long as the current and the part surface area are known, so you can input the current density).
Rearranged once again, the expected thickness after a given time of anodization can also be calculated:
thickness (mils) = time * current density / 720
This product of time and current density is used to calculate thickness and is illustrated in Figure 2 below:
Anodization chart for film thickness.
Image Credit: https://www.floridafinisherscorp.com/
The thickness of the film produced during this time of anodization is calculated by the total area under the curve.
Why Is the 720 Rule Important for Anodizing?
The 720 rule is important for anodizing because it provides a way to predict anodization thicknesses and make your results repeatable. The quality and durability of the final aluminum part may be heavily dependent on the thickness of its anodized layer. The 720 rule predicts a specific time (in minutes) that will be required to achieve your desired film thickness, within an acceptable tolerance (generally ±0.02 mils). The alternative is to periodically stop the anodizing process to measure the film’s thickness, but that is disruptive and will not provide repeatable results.
What Are the Limitations of the 720 Rule for Anodizing?
The 720 rule provides a good estimate for anodizing time across a range of aluminum alloys and electrolyte compositions, but it does have limitations. It is only valid when using a constant-current anodizing process. The 720 rule cannot be applied when different material chemistries affect the anodizing process. This is true of highly alloyed aluminum such as 2024 and 7075 and is also true of other materials such as titanium. The temperature of the electrolyte bath also has an impact on anodizing time which the 720 rule does not account for. Temperature affects the dissolution of electrolytes and therefore affects the rate of the anodizing reaction.
What Is the Standard Anodizing Control for the 720 Rule?
The most basic control factor is to maintain a constant current density for the entire anodization process. With constant-current anodizing, the voltage varies over time to ensure that the part receives an unchanging amount of electrical current as the anodized film grows. Constant current provides a constant rate of film growth. The 720 rule is used to calculate the rate of that film growth (thickness per unit time) based on your chosen current density. Therefore, a selected current density will determine the time required to achieve a specific film thickness.
Some example results are shown below in Table 1, where the rate of film growth (time required to achieve a thickness of 1 mil) is listed according to current density:
Current Density (A/ft^2) | Time to 1 mil (min) |
---|---|
Current Density (A/ft^2) 12 | Time to 1 mil (min) 60 |
Current Density (A/ft^2) 18 | Time to 1 mil (min) 40 |
Current Density (A/ft^2) 24 | Time to 1 mil (min) 30 |
Current Density (A/ft^2) 30 | Time to 1 mil (min) 24 |
Current Density (A/ft^2) 40 | Time to 1 mil (min) 18 |
Table Credit: https://www.floridafinisherscorp.com/
What Is the Process of Anodizing Aluminum?
The process of anodizing aluminum is fairly simple, and can even be recreated at home.
- Pre-treatment: It is crucial to thoroughly clean the aluminum part before anodization. This is usually done with a degreaser and then a pickling solution. The surface finish of the aluminum also has an influence on the anodizing results.
- Anodizing: The aluminum part is submerged in an electrolyte bath (usually chromic or sulphuric acid) and a current is passed through it. The aluminum acts as the anode and a controlled formation of oxide occurs on the surface of the part.
- Coloration: Color can be added to the anodized surface, either by adding dyes or depositing metal salts in the pores of the aluminum oxide.
- Sealing: The final finishing step is to seal the pores by submerging the part in another bath. This can be hot water or a room-temperature nickel and fluoride solution.
This process of anodizing aluminum provides a number of benefits. The metal’s durability and corrosion resistance is drastically improved since the resistant barrier is integrated into the material surface. The aesthetics of aluminum can also be significantly altered with various colors and finishes. These colors are permanent. For more information, see our guide on Everything You Need to Know About Aluminum Anodizing.
Can I Anodize Cast Metals?
Not all cast metals can be anodized. Cast aluminum can be anodized, but it is difficult and often creates an unappealing surface finish. The main challenge is that cast aluminum tends to contain a lot of impurities — particularly silicon. It is crucial to prepare the cast part by de-ashing before anodizing. The surface impurities will interfere with the anodized layer’s consistency; silicon in particular makes the anodized film dark. Further, cast parts tend to be more porous, and these pores do not anodize well. High-quality castings with low porosity and few impurities will minimize these issues and enable a reasonable anodized finish.
Can Anodized Aluminum Have Color?
Yes, it is easy to color aluminum while it’s being anodized. One common method to color aluminum during anodizing is to submerge the part in a metal salt bath. The metal salts settle into the pores of the aluminum oxide on the part’s surface. Another method is to apply a dye after anodizing so that the dye infiltrates the pores instead. The colored part should then be sealed with hot water to form hydrated aluminum oxide crystals that seal the pores. Many colors are possible, such as gold, bronze, or black.
Is the 720 Rule Applicable to Anodized Titanium?
No, the 720 rule cannot be applied to titanium. The anodization of titanium uses different chemical parameters compared to the process for aluminum. The 720 rule applies to most alloys of aluminum, but not to other metals. Generally, titanium anodization can be carried out in seconds, rather than the minutes that aluminum needs.
Summary
This article presented the 720 rule for anodizing, explained what it is, and discussed its benefits and how its implemented. To learn more about anodizing, contact a Xometry representative.
Xometry provides a wide range of manufacturing capabilities and other value-added services for all of your prototyping and production needs. Visit our website to learn more or to request a free, no-obligation quote.
Disclaimer
The content appearing on this webpage is for informational purposes only. Xometry makes no representation or warranty of any kind, be it expressed or implied, as to the accuracy, completeness, or validity of the information. Any performance parameters, geometric tolerances, specific design features, quality and types of materials, or processes should not be inferred to represent what will be delivered by third-party suppliers or manufacturers through Xometry’s network. Buyers seeking quotes for parts are responsible for defining the specific requirements for those parts. Please refer to our terms and conditions for more information.
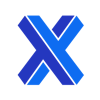