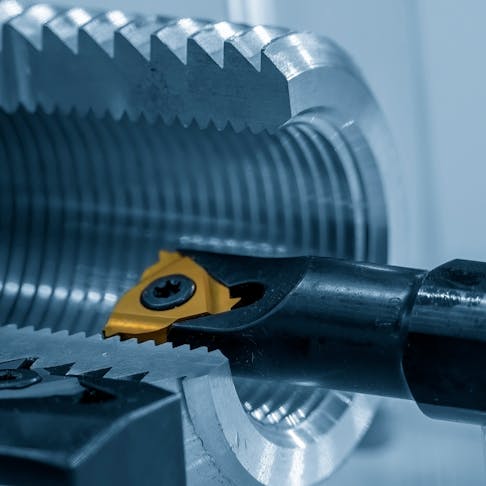
Thread Milling: How It Works, Types, Advantages, and Disadvantages
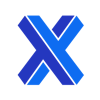
Thread milling is a versatile process used to thread a huge variety of hole sizes, particularly larger diameter holes. It has some similarities to tapping but differs from tapping in that the tool is meaningfully smaller than the hole to be threaded. Thus the tool moves in a circular path around the circumference of the hole to cut the thread.
This article will discuss what thread milling is, how it works, the types, advantages, and disadvantages.
What Is Thread Milling?
Thread milling is a method for cutting threads into a part or workpiece, but with a tool that has a limited contact area with the workpiece. For internal threads inside holes, the thread milling cutting tool has a smaller diameter than the hole and rotates at a relatively high speed as it moves in a circular path around the circumference of the hole. In this way, thread milling is different from tapping, as a tapping tool has a diameter that matches the hole to be threaded, and is in contact with the workpiece along its entire circumference while tapping the hole.
What Is the Function of Thread Milling?
The function of thread milling is to cut a thread into a workpiece. It is typically used for cutting threads inside holes, but can also be applied to cutting threads on the outside of parts. A thread milling tool has a set thread pitch (number of thread crests per inch) but can be used to create left-hand or right-hand threads, and for various flank angles.
What Is Thread Milling Used For?
Thread milling is used mainly for cutting threads in materials that do not have good machinability. For softer materials or materials that are easily machined, conventional tapping would usually be used to cut threads into holes. Thread milling is also used for threading large diameter holes, or for threading to the bottom of a blind hole. These are applications in which tapping has weaknesses or is unable to be used. Thread milling has the flexibility to be used to thread the outside surface of an item as well.
How Does Thread Milling Work?
Thread milling works by using a cutting tool with a toothed profile that rotates relatively quickly. The spindle holding the tool moves in a circular path in the horizontal x-y plane, with a constant, low speed of vertical z movement. In this way, each rotating tooth of the cutting tool cuts a thread that progresses in the z direction through the hole. The thread can be completed in a single pass, or commonly in two (vertical) passes.
How Does Thread Milling Differ From Other Milling Types?
Many different types of milling have been developed, and each type uses its own milling tools to remove material and shape the workpiece. Thread milling uses toothed cutting tools that are different from other milling tools. Some types of milling can be performed manually by moving the cutting tool using handwheels, but other types must be performed using a CNC milling machine. Thread milling requires the use of a CNC milling machine, as there are three coordinated movements of the tool to the workpiece. The tool has a constant rotational speed, and it moves at a constant z-axis (vertical) progression while having a circular path in the x-y (horizontal) plane to cut threads. Some other milling types require rotation of the tool together with movement predominantly in only one direction with the workpiece, such as end milling.
What Are the Types of Thread Milling Cutters?
Just as the holes that may exist in components are varied, the thread mill cutting tools are also varied. Different designs of cutters are suitable for different applications. Three main types are explained below:
1. Straight Flute Thread Mills
These cutters have flutes between the cutting teeth that evacuate the chips. The flutes are straight (rather than at a helical angle). This means that each successive set of teeth engage the workpiece simultaneously, and therefore have relatively high levels of engagement with the workpiece material. This limits the speeds and feeds that can be used, and therefore this type of cutter is generally better suited to materials that are easy to machine. They tend to be the type of cutter best suited to general-purpose projects.
2. Helical Flute Thread Mills
Helical flute thread mill cutting tools have multiple rows of teeth, with flutes around the circumference to assist in evacuating chips. However, these flutes progress helically around the tool, usually at a 15-degree angle or a 30-degree angle. This helical arrangement of the flute reduces cutting side pressure by staggering the engagement of the teeth with the workpiece. It is best suited to high-speed milling.
3. Single Profile Thread Mills
Single profile thread mill cutters have a single tooth with which to cut the thread, with multiple flutes. A variation can have two rows of teeth. This type of cutter completes a thread much slower as it only cuts a single thread per revolution. However, the benefit of cutting a single thread is that much lower torque is needed on the tool, and less heat is generated. This type of thread milling cutter is therefore best suited to materials that are difficult to machine. It is the most versatile type of cutter.
What Are the Advantages of Thread Milling?
Thread milling holds several advantages over tapping. These include:
- A single thread milling cutting tool can be used to create inside and outside threads, left- and right-hand threads, and threads of different diameters.
- Because a thread milling cutter is not in contact with the workpiece along its entire circumference (like a tap would be), the engagement with the material to be cut is significantly lower. Therefore a lower power and torque is required to drive the tool.
- Due to the lower engagement with the workpiece, the wear on the thread milling cutting tool is significantly lower than an equivalent tap.
- Thread milling can be used on materials that are difficult to machine. Particularly for these materials, single tooth cutters could be used, to limit the forces to the minimum. This limits distortion of the workpiece, as well as chatter and risk of breakage of the tool.
What Are the Disadvantages of Thread Milling?
Thread milling is not well suited to every application. Listed below are some of its disadvantages:
- In some applications, the main drawback of thread milling is that it is slower than tapping. If the hole can be threaded easily and reliably with a tap, then thread milling will simply take longer to complete that thread.
- More sophisticated machinery is required for thread milling compared to tapping. A CNC machine is essential for thread milling, it cannot be carried out without one.
How To Choose Thread Milling Cutters?
There are a few factors that influence the choice of thread milling cutter for a part production run. The first is the size of the batch to be produced. If it is a large batch, then speed will likely be an important factor, but with smaller batches, it is less important. With smaller batches, a cost-effective thread mill cutting tool could be used, even if slower feeds and speeds are required.
Second, the diameter of the hole may dictate whether to use an indexable tool or a full carbide tool. Indexable tools have removable carbide cutting inserts so that only the small cutting surfaces need to be replaced, rather than the whole tool. For larger diameters, using an indexable tool is usually more cost-effective than using a full carbide tool, where the whole tool needs to be replaced once it is worn.
The depth of the hole to be threaded is a third factor to consider. Particularly deep holes would take a very long time to thread using a single profile cutter, and therefore a multi-tooth cutter should be considered. Finally, the material being threaded will influence the best substrate and coating to choose for the cutting tool.
What Is the Importance of Choosing the Right Thread Milling Cutters?
It is important to choose the right thread milling cutter as it will ultimately affect the cost-effectiveness of producing each part. Selecting the incorrect tool will cost a workshop in two main ways. Either the tools will wear out and need frequent replacement (causing additional cost and standing time), or the time taken for thread milling will be longer than optimum, hindering the production rate. It is also possible to damage and scrap a part if the incorrect thread milling cutter is chosen, as the threads can be cut poorly and render the part unusable.
How Does the Choice of Thread Milling Cutter Affect Its Performance?
The choice of thread milling cutter will affect its performance in speed, quality, and cost-effectiveness. Time is money, and a shorter production time will always benefit a machine shop. Choosing the right thread milling cutter will allow the optimum production time to be achieved, with relatively high feeds and speeds without prematurely shortening the tool’s life. Extending tool life supports overall cost-effectiveness. A cutter should be selected for the hole and material to be threaded so that it does not experience excessive wear while still being able to thread at a reasonably high speed. This also affects quality. Heat buildup during threading can cause distortion, and other effects such as chatter and chip hammering can result in poor-quality threads.
How Can Xometry Help in Choosing the Right Thread Milling Cutter?
Xometry can help in choosing the right thread milling cutter through our team of in-house manufacturing specialists. Xometry can help customers source specialist materials and manufacturing processes for their parts, and our in-house specialists have the experience to advise on the best thread milling cutting tool to use for a particular material and geometry.
How To Thread Mill?
The first step to thread milling is understanding the application, the material to be milled, and the geometry of the hole to be milled (depth, diameter, and desired thread dimensions). This allows the second step to be taken which is to select the best thread mill cutting tool for the job. Thirdly, the CNC programming must be undertaken. This programming is informed by calculations for the radial depth of cut and the acceptable feeds and speeds. To complete the programming, however, it is recommended to use CAD/CAM software for thread milling. Once this has been completed, it is best to set up a trial piece, to test the tool-path feeds and speeds without the risk of damaging a production part. Once the test has been completed satisfactorily, the production run can start.
What Are the Tips for Thread Milling?
Each thread milling application will take experience to set up the optimal CNC path. Listed below are some tips for thread milling:
- Pay attention to tool wear and thread quality to make the right adjustments.
- Use slower cutting speeds whenever possible.
- Ensure that there is sufficient flow and pressure of coolant, to maintain a safe temperature at the cutting surface and to assist with evacuating chips.
- Ensure that the workpiece is clamped securely. This will mitigate the risk of vibration during thread milling.
- If tool wear is noticed at the cutting edges, it may be worth adjusting the approach of the tool through the thread. Climb milling, starting to thread from the bottom of a hole rather than the top, or using additional radial passes can assist in extending tool life.
How Do Thread Milling and Tapping Differ?
Thread milling and tapping differ in several ways. The most fundamental is that a thread milling tool is a smaller diameter than the thread to be tapped, whereas, with a tap, it matches the diameter of the thread. This means that a tap is engaged with the workpiece around its full circumference, and therefore needs a higher torque to be driven. However, the thread mill cutter, being a smaller diameter, is only engaged at one portion of its circumference and rotates at a high speed as it moves in a circular path around the edge of the hole being threaded. In this way, it requires a much lower torque. Also, larger holes of various diameters can be threaded with one tool, whereas a tap can only be used to thread a single-diameter hole.
To learn more, see our article on how Thread Milling and Tapping Differ.
Is Thread Milling Better Than Form Milling?
No, thread milling is not better than form milling, the two types of milling simply have different applications. Thread milling is used to cut threads into a workpiece, in which the features of the threads (the crests for example) are typically less than 1/8th of an inch apart. These are also multiple repeating features. Form milling is used to cut particular profiles into the surface of a workpiece, but these contours are typically larger than threads, and also only a single (or few) profiles adjacent to each other. Thread milling and form milling are both valuable processes for introducing particular profiles into a workpiece, but they introduce very different profiles and therefore have different applications.
What Is a Thread Mill Calculator?
A thread mill calculator is a simple piece of software that gives recommendations for parameters in a thread milling setup. It can be an online calculator, a spreadsheet file, or a portion of a sophisticated software package. It takes in data of the hole to be threaded, performs the relevant calculations, and provides the starting points for the CNC programming to carry out the threading. For instance, a thread mill calculator estimates the allowable chip loading and speed of the tool.
How Does a Thread Mill Calculator Work?
A thread mill calculator works by taking key dimensions of the thread to be achieved, processing those through some fairly simple equations, and outputting a series of suggested parameters for the mill programming. Thread mill calculators allow all the mathematical relationships in milling—inputs to outputs—to be displayed in an easy-to-use tool without having to spend too much time with the math in between.
What Is the Importance of a Thread Mill Calculator?
A thread mill calculator is important as it provides recommendations for key parameters of the milling setup. It is very useful to have starting points for these parameters when preparing the CNC programming. Although the results of the calculator may not be the final parameters, they should be fairly close and will be a good starting point to adjust from. Without using the mathematical relationships in a thread mill calculator, the setup would rely fully on the feel and experience of the operator, or worse—trial and error.
Is a Thread Mill Calculator Accurate?
Yes. A thread mill calculator should be used as a guide to provide a good starting point for the relevant settings. Each job needs to be evaluated independently, and experience is invaluable in choosing the milling setup. The results of a thread mill calculator should not be applied blindly—the quality of the threads produced, and the wear on the cutting tool should be used to inform adjustments to the calculator’s suggested setup.
Summary
This article presented thread milling, explained it, and discussed how it works and its advantages. To learn more about thread milling, contact a Xometry representative.
Xometry provides a wide range of manufacturing capabilities, including machining and other value-added services for all of your prototyping and production needs. Visit our website to learn more or to request a free, no-obligation quote.
Disclaimer
The content appearing on this webpage is for informational purposes only. Xometry makes no representation or warranty of any kind, be it expressed or implied, as to the accuracy, completeness, or validity of the information. Any performance parameters, geometric tolerances, specific design features, quality and types of materials, or processes should not be inferred to represent what will be delivered by third-party suppliers or manufacturers through Xometry’s network. Buyers seeking quotes for parts are responsible for defining the specific requirements for those parts. Please refer to our terms and conditions for more information.
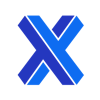