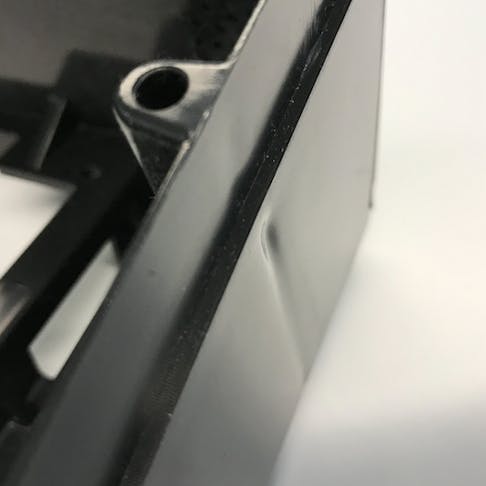
Managing Sink in Injection Molding Designs
Reduce divots and see-thru marks on your molded part with these tips.
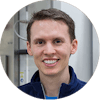
A thick section between a boss and the outer wall causing significant sink marks
Sink is one of the most common cosmetic defects in injection molded parts, and is characterized by surface depressions, often in sections with thick walls. This is caused by the uneven shrinking of material as it cools, when thicker cross-sections of a part pull more than the thinner areas when hardening from liquid to solid, leaving divots on the opposite side.
An example of this is when there are ribs or boss (screw mount) features on the opposite side of a cosmetic face. Sink from ribs will appear as lines or a grid impression, and a boss may make little dips akin to a doughnut shape.
Ways to Mitigate Sink
Sink is not inherently bad. But if the part has cosmetic requirements, it may be unappealing. The good news is that sink can usually be mitigated through best design practices. Here are three go-to rules for managing sink in your next injection molded project.
1. Make all your outer walls uniform.
This design strategy, in addition to designing internal ribs that are 40-60% of the outer wall thickness, will help manage sink in your injection molded parts. To see this in practice, take a look at a LEGO or pop off the battery cap of your remote to see this in practice. The outer wall of a part is its primary structure, and also where the material will flow with the least resistance—filling the part cavity in the mold. Ribs are used to add strength and rigidity without adding excess thickness. However, note that ribs that are the same thickness as a wall tend to show more sink because they are pulling material away from the wall and into the rib when cooling. By making ribs thinner than the outer walls, the outer walls will actually stay more stable than the rib, which will significantly reduce sink marks.
2. Cut some material away from boss features.
This is a really interesting trick that can remove visible rings from a cosmetic face. A boss is a cylinder extruded out, typically perpendicular, from a surface. It has an interior hole which will usually accommodate a thread, an insert, or a screw for assembly.
Using the rule above, the boss should have a nominal thickness of 40-60% of the outer wall. In addition, the thickness ratio between the internal blind hole and the outer wall should be at the same 40-60% range. The last feature is a triangular groove around the boss which is 30% of the wall thickness deep and merging back to the outer wall at a 30-degree angle. These additional cuts reduce and move the points of mass which would traditionally pull material while cooling, thus mitigating sink marks.
Removing material around a boss will reduce the see-thru of sink on the opposite side
3. Adding texture to the cosmetic surface.
Even with best design practices, there may still be faint sink marks visible on the surface. Using a matte surface finishing such as mold texturing (MT-11010, MT-11020, or the equivalent), or SPI matte finishes like C3 to D3, will help hide any remaining sink marks by reducing glare pick up from minor imperfections.
A small circular sink line between the two holes of this part are barely visible against the matte texture
Xometry has a vast number of resources to help you get parts through its online injection molding service. This includes a detailed design guide and live engineering support to get free and direct help on your injection molding quote. Xometry also provides high quality medical injection molding services.
FREE Injection Molding Design Guide
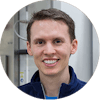