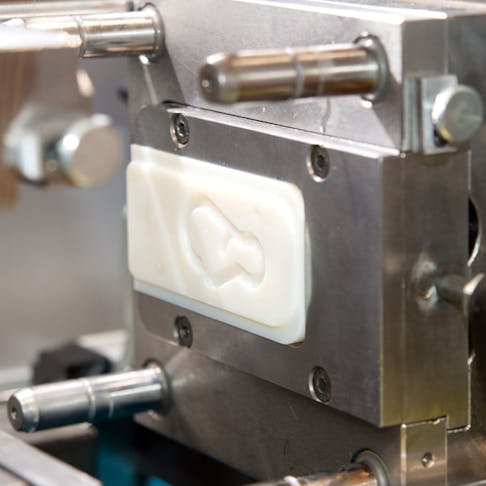
Injection Molding Defects and How to Prevent Them
Learn about 11 of the most common defects encountered in injection molding.
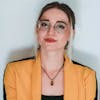
Injection molding is a manufacturing technique that enables fast and large-scale production of components used in a large variety of industries. Due to the delicacy of this process and its wide application, there's a wide range of mistakes in the injection molding process that can lead to defects in the injection molded products. This article will go through the types of defects in injection molding and how to prevent them.
1. Burn Marks
This injection molding defect appears as black or rust-colored discoloration on the molded part's surface or edge. Like flow lines, burn marks do not usually compromise the item's integrity, but they may become a problem once the product is burnt to the point of degradation.
Burn marks are most commonly caused by the overheating of trapped air bubbles or resin in the mold during the injection. This happens due to either high injection rates or excessive heating of the material itself.
The most important prevention method for this defect is to reduce the melt and mold temperature, as well as the injection speed, of the molding tool. Moreover, manufacturers can avoid burn marks by adding exhaust systems and expanding the gas vents so that trapped air can escape easily during the low-pressure injection. Last but not least, they might try to shorten the molding cycle time (the injection and cooling time) so any trapped air or resin does not overheat.
2. Surface Delamination
Surface Delamination is a surface layer flaking defect that occurs when thin layers on the surface of a molded component readily separate or peel away from the underlying material. Since it reduces the component's strength, it is generally regarded as a serious problem for a finished product.
The most prevalent cause of delamination is foreign material contamination of the resin pellets or other base material. When two materials cannot adequately bind to each other, flaky separation occurs. Aside from the material injected into the hopper, any extra release agents covering the mold for better component separation might potentially be contaminated. Delamination can also be caused by excessive moisture on the material due to insufficient drying before usage.
There are various ways to prevent delamination, depending on what caused it. First of all, resin pellets must be appropriately stored and handled at all times. If release agents are the problem, the manufacturer should try to decrease the reliance on them by redesigning the mold and emphasizing the injection nozzle. In case of excess moisture, the mold temperature should be increased, or the material should be adequately pre-dried.
3. Vacuum Voids
Vacuum voids occur in injection molding usually as a result of having an insufficient amount of plastic material injected into the mold. The root cause is sometimes related to what is termed a short shot, where the molding injection step did not introduce a sufficient amount of plastic into the mold to completely form the part. As the plastic material cools, it shrinks and can leave an empty space within the molded product's body.
Another potential cause of vacuum voids is the formation of gas pockets in the plastic material within the mold. There are several ways in which gas bubbles may form in the plastic material, which are:
- Poor venting causes air to remain in the mold instead of being replaced entirely by the plastic.
- Water in the mold vaporizes within the plastic resin and causes pockets to form.
- Volatile compounds which are part of the resin mixture form into a gas as the plastic resin is heated.
- Excessive heating during the injection molding process deteriorates the plastic resin and introduces gas into the plastic resin
Troubleshooting should focus on identifying the underlying cause of the vacuum void and then adjusting the process by changing injection pressure, cooling rate, runner or gate size, or making design changes to the mold itself to reduce shrinkage of the plastic resin.
4. Discoloration
When a molded object has a different color than expected, it is referred to as discoloration or "color streaking." This defect is often restricted to a small region or a few streaks of abnormal color. Even though discoloration does not affect the product's strength, it does affect its aesthetics.
Residual resin in the nozzle, stale pellets in the hopper, or a mold from a previous production run are all common causes of discoloration. Other probable factors include poor heat conductivity of the coloring component or improper masterbatch mixing.
To make sure discoloration doesn't happen, residual resins or ingredients should be eliminated by ensuring that the machine, hopper, nozzle, and mold are cleaned correctly between each manufacturing cycle. The manufacturer should ensure that the color agent used has excellent heat conductivity (in other words, that it can withstand high temperatures). Furthermore, the masterbatch should be equally blended to ensure consistent color output.
5. Warping
Warping happens when different sections of the molded part shrink disproportionately. Plastic and other materials can warp during the cooling process like wood does when it dries unevenly. As a result, the shape of the item is twisted, uneven, or curved in places where it wasn't supposed to be.
Premature or rapid cooling is a major cause of warping. Excessive warmth and a material's low thermal conductivity can also lead to warpage. In other cases, since the shrinkage increases proportionally with wall thickness, the mold design is to be blamed for this type of defect.
To prevent warping from happening, the cooling process should be gradual and lengthy enough to allow the material to cool without warping. Additionally, it's essential to know which type of material to use. Some materials are less prone to shrinking during cooling, such as particle-filled thermoplastics, unlike semi-crystalline materials or unfilled grades. Another solution would be to redesign the mold with consistent wall thickness and symmetry. This will achieve better component stability during cooling.
6. Flash
Flash, also known as "burrs" or "spew," is an excess of molding material that appears as a protrusion at the component's edge. Flash happens when the material flows outside the specified flow channels and into the gap between the tooling plates or the injector pin. Even though this defect is subtle most of the time, it can become a significant problem if it is visible.
Flash can occur when the mold isn't clamped tightly enough, so plastic seeps through the cracks; it must be strong enough to withstand the opposing pressures created by the molten plastic flowing through the mold. If the injection pressure is too high, plastic will be forced out into the path of least resistance. However, the primary cause of this injection molding defect is poor mold condition or maintenance.
Flashes can be prevented by increasing the clamping force on the plate to keep the material in the channel. Other methods include increasing the material flow, as well as adjusting the mold temperature, injection pressure, and ventilation. Moreover, repairs and maintenance should be regularly performed to keep the mold in working order.
7. Sink Marks
Sink marks are small depressions or craters that appear on the thicker parts of a part's otherwise flat surface. They commonly occur when the interior of a molded component shrinks, which causes the material to pull from the outside inward.
The main reason for these defects is insufficient cooling time or the cooling mechanism for the plastic to properly cool and cure while in the mold. Inadequate mold cavity pressure or a high temperature at the gate can also cause sink marks. As mentioned, these mostly appear on thicker parts, since thicker areas of the injection molded part take longer to cool than thin ones.
Several different steps may be taken to prevent sink marks from appearing. First of all, the cooling time should be increased to reduce shrinkage. Next, the thickness of the thickest wall parts should be reduced, thus providing shorter cooling times. To allow for more sufficient cooling and curing, mold temperatures should be reduced, holding pressure increased, and holding duration extended.
8. Weld Lines
Weld lines, also called knit lines, are a defect that occurs with molded parts caused by two different flows of plastic resin that do not adequately join together or weld together correctly during injection molding. When the resin is injected into a mold, there are areas where the resin needs to flow around an obstruction in the mold that is intended to form a feature of the finished part. Ideally, the resin flow will split into two flow fronts to pass around the obstruction and then recombine into a single flow front. When this fails to happen correctly, a weld line defect occurs.
There are several possible causes that need to be investigated to troubleshoot weld lines in injection molding. These potential causes include:
- Inadequate injection pressure impeding resin flow
- Lower process temperature causing premature solidification of plastic in some areas of the mold
- Slow resin flow through the mold resulting in non-uniform cooling
- Resin impurities that result in flow speed variations within the mold
- Excessive material is injected into the mold, causing a slowdown in flow speed
- Mold design issues such as improperly placed gates or inadequate wall thickness
Corrective measures to consider include increasing injection pressure, adding hot runners to the mold, mold redesign to adjust the number of gates and their location, or changing the type of resin being used to create improved resin flow within the mold.
9. Jetting
Jetting is a defect that occurs on the surface of injection molded parts which has the appearance of a serpentine or squiggly line similar in appearance to that of a worm track. Jetting is caused when the resin is injected too rapidly into the mold through an area or restricted flow such as a gate or runner. The flow of resin enters the mold cavity with a spray pattern that is back and forth, creating a snake-like stream of material that begins to cool before the balance of the melt can fill the mold. This cooling results in a failure of the material to properly weld together leaving behind the defect that is referred to as jetting.
The basic underlying causes of jetting are related to one or more of the following:
- How the resin shot is flowing in the mold
- The speed at which the resin is injected
- The temperature of the resin
Troubleshooting should focus on examining gate placement and gate diameter to avoid mold injection into the center of the mold cavity. Additional actions to take include examining the ram speed setting and reducing it as needed, or using hot runners or a heated mold to address issues with premature cooling of the plastic resin. Lastly, a review of the resin being used and alternatives should be performed to compare their characteristics and performance in particular with respect to mold temperature and cooling rate.
10. Flow Lines
Flow lines are stains, patterns, or lines that appear on thinner areas of the molded component, frequently of a slightly different color than the surrounding area. They can also appear on a product's surface as ring-shaped bands near the mold's entry points. Even though flow markings usually don't affect the component's integrity, they are undesirable for products that must be appealing to the eye.
One of the leading causes of flow lines is the variations in the material's cooling rate as it flows in different directions within the mold. Another reason is wall thickness – if there is no uniform thickness of the walls, the material cools and solidifies at different speeds. Moreover, a slow injection speed or low-pressure molding can also cause unwanted flow lines.
One solution is to make sure that the material fills the mold before cooling. This can be done by increasing the pressure, speed, and material temperature to the recommended optimal level. In addition, manufacturers will round corners and points where the wall thickness varies to avoid abrupt changes in direction and flow rate. To prevent the material from cooling too quickly, mold gates (the openings through which the polymer solution is fed into the final item) can be relocated farther from the mold coolant (used to regulate and reduce the temperature in the mold).
11. Short shots
As the name indicates, short shots are scenarios in which the plastic shot into the mold stops short of reaching everywhere within the mold. These defects can be one of the most severe injection molding defects since they may drastically alter the desired look of the molded object or prevent it from performing its intended function. Short shots happen when the material cannot fill the mold's cavities, resulting in an incomplete product once it completely cools down.
A variety of factors might result in short shots. If the shot is incorrectly calibrated, the plastic material may be insufficient to fill the voids. If the plastic is overly viscous, it may harden before filling all of the holes, resulting in a short shot. In case of inadequate degassing or gas venting methods, trapped air has no way to leave, and the plastic material cannot occupy the area that air or gas already occupies, which again results in short shots.
One of the most common solutions for this defect is to enhance the flow of the material through the mold. This can be done by either redesigning the mold with broader channels and gates, increasing the injection speed and pressure, or by using a thinner base material. To keep the material from cooling too quickly, the temperature in the mold should be increased. Moreover, more air vents should be added or existing ones widened so trapped air can better escape. It's also important to use plastic that is less viscous and has better flowability so that it can fill the hardest-to-reach cavities.
How To Prevent Injection Molding Defects
Preventing plastic injection molded part defects can be as simple as correcting the injection molding process. Defects may also be prevented by replacing production equipment or redesigning mold tooling. Molding defects often caused by process problems include burn marks, vacuum voids, warping, sink marks, weld lines, jetting, and flow lines.
Burn marks are prevented by reducing the melt and mold temperature and the injection speed. Vacuum voids can be stopped by changing the injection pressure, cooling rate, runner or gate size, or redesigning the mold to reduce the shrinkage of the plastic resin. Warping and sink marks are prevented by ensuring the cooling process is gradual.
Weld lines can be prevented by increasing injection pressure, adding hot runners to the mold, or redesigning the mold to adjust the number of gates and their location. Jetting can also be prevented with a mold redesign. Preventing flow lines means preventing the material from cooling too quickly, with mold gates relocation an important consideration.
Molding defects related to material use or storage include surface delamination and discoloration. Delamination is prevented by the appropriate handling and storage of resin pellets. Discoloration is prevented by ensuring that the machine, hopper, nozzle, and mold are cleaned correctly between each manufacturing cycle.
Injection molding defects caused by faulty mold design or poor maintenance include flash and short shots. Flash is prevented by increasing the clamping force on the plate to keep the material in the channel. Short shots can be avoided by enhancing the flow of the material through the mold.
What Are the Disadvantages of Using Injection Molding?
While injection molding has many advantages, it also has some disadvantages. The disadvantages of injection molding are the high initial cost, the long initial lead time, the size limitations, and the necessary careful designs.
- High initial cost: Several rounds of designing and modeling are often needed before the go-ahead for production is given. Then, the injection molding tool will require designing and manufacturing. The mold tool is an intricate piece of work whose costs include staffing, material, and many machining hours to fabricate and check the mold. This detailed work makes mold creation the highest upfront cost in preparing to perform injection moldings. But, of course, once the mold and machine are done, the part cost of injection molding is very low, and the repeatability is very high for hundreds of thousands of moldings.
- Long initial lead time: Injection molding has a longer lead time and often takes 5-7 weeks to manufacture tooling and 2-4 weeks to produce and ship parts. This long lead time is partially because of the complexity of the molds. These molds have complex runner and water cooling systems to facilitate material flow and faster cooling. As a result, some molds require months of design and testing, and any design changes can further increase turnaround times.
- Size limitations: The weight and size of the part will determine the tool size and necessary press size. Plastic injection molding machines are already large, and the larger the part, the larger the machine needed, and the more difficult and expensive the molding process will be. Huge parts need an enormous mold tool and are very expensive to make.
- Careful designs: Parts must be designed with injection molding process considerations in mind and must follow the basic rules of design for injection molding. For example, undercuts and sharp edges must be avoided as much as possible, and uniform wall thicknesses must be used. These design rules somewhat complicate the process of designing a part that is planned to be injection molded.
Summary
This article presented some of the common molding defects that can happen during injection molding and how the manufacturer should fix and prevent them. More specifically, these defects may be caused by various factors, ranging from the inadequate tuning of the parameters to the wrong choice of material or poor mold design.
Xometry's industry experts and vetted network of manufacturers can help you avoid running into some of these issues. If you have an upcoming injection molding project, feel free to start a quote today! You can have your own custom plastic molded prototypes and production parts in as few as 10 business days.
Disclaimer
The content appearing on this webpage is for informational purposes only. Xometry makes no representation or warranty of any kind, be it expressed or implied, as to the accuracy, completeness, or validity of the information. Any performance parameters, geometric tolerances, specific design features, quality and types of materials, or processes should not be inferred to represent what will be delivered by third-party suppliers or manufacturers through Xometry's network. Buyers seeking quotes for parts are responsible for defining the specific requirements for those parts. Please refer to our terms and conditions for more information.
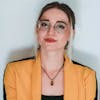